Validating Tension on an "Awkward-to-Torque" Bolt
#1
Le Mans Master


Thread Starter

I have a critical application that has just enough room to permit
installation of a button head, hex socket cap screw into a blind hole.
However, there is not enough room to torque it straight through the
axis and it is impractical to relieve the obstacle to provide clearance.

One solution I have thought of is to use a ball-end hex bit socket.

This tool provides enough off-set to clear the obstacle, but raises the
question about what difference there is between actual torque applied
to the fastener, relative to the torque indicated on the TQ wrench?
As mentioned the bolt goes into a blind hole. The only test I have
been able to devise is to mock up an open-ended fixture that allows me
to measure bolt stretch. The idea being to tighten sample bolts by
applying torque straight down the axis and at an angle, recording the
stretch and comparing to see whether any difference occurs.
Are there any pitfalls to be aware of in using such a stretch test to
correlate in-line application of torque against angular application?
What about other ideas for ensuring that the desired torque is applied
and loosening of the fastener is prevented?
I am unaware of a secure method of safety-wiring a button-headed
cap screw.
One idea has been to grind a flat on the side of the head and make a
strip with locking tabs (such as are used on certain 2-pc hat/rotors and
for retaining ring gears to differential units.)
I am not confident that thread locking compound can be used
satisfactorily. Operating temperatures in the vicinity of the fastener
are 250-300ºF and can spike over 300ºF at times. This exceeds the
recommended temp range for conventional blue and red thread lock
compounds (-65°F to 300°F). It gets WELL into the upper range of
high-temp red versions of threadlockers (-65°F to 450°F).
Thanks,
Ken R.
.
installation of a button head, hex socket cap screw into a blind hole.
However, there is not enough room to torque it straight through the
axis and it is impractical to relieve the obstacle to provide clearance.

One solution I have thought of is to use a ball-end hex bit socket.
This tool provides enough off-set to clear the obstacle, but raises the
question about what difference there is between actual torque applied
to the fastener, relative to the torque indicated on the TQ wrench?
As mentioned the bolt goes into a blind hole. The only test I have
been able to devise is to mock up an open-ended fixture that allows me
to measure bolt stretch. The idea being to tighten sample bolts by
applying torque straight down the axis and at an angle, recording the
stretch and comparing to see whether any difference occurs.
Are there any pitfalls to be aware of in using such a stretch test to
correlate in-line application of torque against angular application?
What about other ideas for ensuring that the desired torque is applied
and loosening of the fastener is prevented?
I am unaware of a secure method of safety-wiring a button-headed
cap screw.
One idea has been to grind a flat on the side of the head and make a
strip with locking tabs (such as are used on certain 2-pc hat/rotors and
for retaining ring gears to differential units.)
I am not confident that thread locking compound can be used
satisfactorily. Operating temperatures in the vicinity of the fastener
are 250-300ºF and can spike over 300ºF at times. This exceeds the
recommended temp range for conventional blue and red thread lock
compounds (-65°F to 300°F). It gets WELL into the upper range of
high-temp red versions of threadlockers (-65°F to 450°F).
Thanks,
Ken R.
.
#2
Race Director



unlike using an impact wrench, where flex can actually limit applied torque, I don't think the extension you show will make much impact on torque readings.
Can't you just screw one of the bolts into a nut (off of the car) with the extension, then re-torque it without the extension and see if it turns any??????
And finally, I've used blue loc-tite in plenty of engine applications in the range you mention, and it's always worked well for me. While it might not meet it's intended vibration resistance, it's always been intact when I've removed the fasteners.
What is the application here.....that might help give some insight....
Can't you just screw one of the bolts into a nut (off of the car) with the extension, then re-torque it without the extension and see if it turns any??????
And finally, I've used blue loc-tite in plenty of engine applications in the range you mention, and it's always worked well for me. While it might not meet it's intended vibration resistance, it's always been intact when I've removed the fasteners.
What is the application here.....that might help give some insight....
#3
Race Director



hey just thinking, but I really don't think the flex of the extension will effect torque. This is just like a torsion spring...so think of a coil spring. If you stand on a set of scales and weigh 100lbs, then stand on top of a spring which is on top of a set of scales, the spring will compress, but you'll still weigh 100lbs. The static force should be the same, although again this would not be true in a dynamic (impact wrench) application.
#4
Le Mans Master


Member Since: Feb 2000
Location: Bedford NH
Posts: 5,708
Likes: 0
Received 1 Like
on
1 Post
Cruise-In II Veteran


Since you cannot use safety wire, perhaps you try a "Nordlock". I normally never use any of the common methods like "Locktite" and I am very, very skeptical (after doing a fastener study at TRW under a USAF contract) of most things other than safety wire, but Nordlocks really work. The big issue is the friction under the head that "eats" so much of the torque and the fastener pre-load is not achieved. These allow the preload almost like a one way thrust bearing. I get mine from Richard Strout at www.lemd.com .
"Tension makes the bolt self-locking
The key is the difference in angles. Since the cam angle " α " is larger than the thread pitch " β ", the pair of washers expand more than the corresponding pitch of the thread. NORD-LOCK washers positively lock the fastener in a joint which is subjected to extreme vibration or dynamic loads. "


http://www.nord-lock.com/default.asp?url=2.16.37
BTW, is this the bearing fasteners you are doing? If so, I am using reduced head 12 point M12's with Nordlocks for that in the blind hole.
"Tension makes the bolt self-locking
The key is the difference in angles. Since the cam angle " α " is larger than the thread pitch " β ", the pair of washers expand more than the corresponding pitch of the thread. NORD-LOCK washers positively lock the fastener in a joint which is subjected to extreme vibration or dynamic loads. "


http://www.nord-lock.com/default.asp?url=2.16.37
BTW, is this the bearing fasteners you are doing? If so, I am using reduced head 12 point M12's with Nordlocks for that in the blind hole.
Last edited by ghoffman; 06-08-2008 at 09:27 AM.
#5
Pro


Member Since: Dec 2005
Location: brooksville , fl 34602
Posts: 746
Likes: 0
Received 0 Likes
on
0 Posts


I do alot of home machine shop work and have never seen these fasteners. They look really practical. It would be nice to know the original op project. Sometimes things can be over engineered!!!

#7
Pro


Member Since: Dec 2005
Location: brooksville , fl 34602
Posts: 746
Likes: 0
Received 0 Likes
on
0 Posts


you read my mind " specialty = $ " kind of like the corvette tax.
Looks like torque could be lowered with this fastener. Someone should show these to GM for the rear axel bolt!!!!!!!!!!!!Cheaper than the tsb. Anyway thanks for a valuable tip; gotta love this forum.

#8
Le Mans Master


Member Since: Feb 2000
Location: Bedford NH
Posts: 5,708
Likes: 0
Received 1 Like
on
1 Post
Cruise-In II Veteran


Yes, I agree! In fact, when you calculate fastener torque, the Fc (friction under the collar, i.e. bolt head) is a major part of the total friction that has to be overcome to get the correct preload in the fastener. These do reduce that going on and increases it when unscrewing it.
Just to be clear, it is just the 2 piece washer thingy that you buy. They come lightly glued together, and can be reused many times as long as you put them back together with the ramps together as shown. The stainless steel versions are about $2 each for a 1/2 size, but the $.50 version is plated and I find that to be fine.
Just to be clear, it is just the 2 piece washer thingy that you buy. They come lightly glued together, and can be reused many times as long as you put them back together with the ramps together as shown. The stainless steel versions are about $2 each for a 1/2 size, but the $.50 version is plated and I find that to be fine.
Last edited by ghoffman; 06-08-2008 at 09:56 AM.
#9
Pro


Member Since: Dec 2005
Location: brooksville , fl 34602
Posts: 746
Likes: 0
Received 0 Likes
on
0 Posts


actually 50cents for half inch isnt bad. Reusable too ; now where to locate is the 64 bazillion $ question. Hmm , sunday morn and my car is calling. Thanks for the info; this should go to each section on the forum!

#10
Le Mans Master


Member Since: Feb 2000
Location: Bedford NH
Posts: 5,708
Likes: 0
Received 1 Like
on
1 Post
Cruise-In II Veteran


Get them at www.lemd.com, 603-772-1835 ask for Richard, and tell him Gary sent you!
Watch this video:
http://www.nord-lock.com/default.asp?url=51.16.37
Watch this video:
http://www.nord-lock.com/default.asp?url=51.16.37
Last edited by ghoffman; 06-08-2008 at 10:08 AM.
#11
Le Mans Master



Since you cannot use safety wire, perhaps you try a "Nordlock". I normally never use any of the common methods like "Locktite" and I am very, very skeptical (after doing a fastener study at TRW under a USAF contract) of most things other than safety wire, but Nordlocks really work. The big issue is the friction under the head that "eats" so much of the torque and the fastener pre-load is not achieved. These allow the preload almost like a one way thrust bearing. I get mine from Richard Strout at www.lemd.com .
"Tension makes the bolt self-locking
The key is the difference in angles. Since the cam angle " α " is larger than the thread pitch " β ", the pair of washers expand more than the corresponding pitch of the thread. NORD-LOCK washers positively lock the fastener in a joint which is subjected to extreme vibration or dynamic loads. "


http://www.nord-lock.com/default.asp?url=2.16.37
BTW, is this the bearing fasteners you are doing? If so, I am using reduced head 12 point M12's with Nordlocks for that in the blind hole.
"Tension makes the bolt self-locking
The key is the difference in angles. Since the cam angle " α " is larger than the thread pitch " β ", the pair of washers expand more than the corresponding pitch of the thread. NORD-LOCK washers positively lock the fastener in a joint which is subjected to extreme vibration or dynamic loads. "


http://www.nord-lock.com/default.asp?url=2.16.37
BTW, is this the bearing fasteners you are doing? If so, I am using reduced head 12 point M12's with Nordlocks for that in the blind hole.

I remember seeing info on these washers many years ago (maybe 10 or 15 years) but had forgotten about them. Always nice to have another alternative when working with fasteners.

#12
Le Mans Master


Member Since: Feb 2000
Location: Bedford NH
Posts: 5,708
Likes: 0
Received 1 Like
on
1 Post
Cruise-In II Veteran


hey just thinking, but I really don't think the flex of the extension will effect torque. This is just like a torsion spring...so think of a coil spring. If you stand on a set of scales and weigh 100lbs, then stand on top of a spring which is on top of a set of scales, the spring will compress, but you'll still weigh 100lbs. The static force should be the same, although again this would not be true in a dynamic (impact wrench) application.

#17
Le Mans Master


Thread Starter

Thank you to davidfarmer for the PMs and thanks to everyone for the
advice & suggestions.
The fastener in question is a M6 x 15 1.00P (roughly similar to the dia
of 1/4" UNC). The application is to attach a custom pickup with a 3/4"
inlet tube to an oil pump. The small size and tight confines precluded
the use of the 'Nordlock' washers suggested by ghoffman.
The issue is (was) that to position the pickup in the desired location,
the fabricator curved the inlet tube to the mounting flange in such a
way that he didn't leave room for a conventional hex or socket head
cap screw. I still do not know what fasteners he used to mock up the
components for brazing. The OD of a hex cap is too large. While a
socket head cap is smaller in dia, its head height interferes where the
inlet tube arcs past overhead of the fastener and flange.
The solution appeared to be to use a button head hex socket cap
screw, but this left the question of how to accurately torque it
because the inlet tube blocks straight access to the socket. It
also meant there was no way to safety wire the capscrew for positive
retention.
A further issue that developed after my initial post is that the
button caps available to me locally were made offshore and I could
not be sure of the level of QA.
My solution has been to:
at an angle. In a pinch, the results from this idea would have been close
enough for my purposes. The bigger issue was trying to determine
what published/recommended torque values to use as a basis - an M6
doesn't take much torque to begin with and since there is some significant
(relative to total TQ) difference of opinion, I just did my own testing.
The net result of the thought and work provides confidence that the
capscrew is adequately torqued to specification and is backed up with
safety wire to hold it in place in the event that something should cause
the torque value to fall off.
Again, thanks for the ideas and support.
.
advice & suggestions.
The fastener in question is a M6 x 15 1.00P (roughly similar to the dia
of 1/4" UNC). The application is to attach a custom pickup with a 3/4"
inlet tube to an oil pump. The small size and tight confines precluded
the use of the 'Nordlock' washers suggested by ghoffman.
The issue is (was) that to position the pickup in the desired location,
the fabricator curved the inlet tube to the mounting flange in such a
way that he didn't leave room for a conventional hex or socket head
cap screw. I still do not know what fasteners he used to mock up the
components for brazing. The OD of a hex cap is too large. While a
socket head cap is smaller in dia, its head height interferes where the
inlet tube arcs past overhead of the fastener and flange.
The solution appeared to be to use a button head hex socket cap
screw, but this left the question of how to accurately torque it
because the inlet tube blocks straight access to the socket. It
also meant there was no way to safety wire the capscrew for positive
retention.
A further issue that developed after my initial post is that the
button caps available to me locally were made offshore and I could
not be sure of the level of QA.
My solution has been to:
- turn a chamfer on the top (wrench side) of a conventional hex
socket capscrew to taper the upper half of the head enough to clear
the inlet tube. - tap an M6 hole in 0.250 material and torque several capscrews using
a ball-end hex bit socket held at a 25º-30º angle from the axis of the
bolt shank to compare bolt stretch against bolts torqued in line with
the axis of the shank. - drill the chamfered head of the hex socket capscrew for safety wire.
at an angle. In a pinch, the results from this idea would have been close
enough for my purposes. The bigger issue was trying to determine
what published/recommended torque values to use as a basis - an M6
doesn't take much torque to begin with and since there is some significant
(relative to total TQ) difference of opinion, I just did my own testing.
The net result of the thought and work provides confidence that the
capscrew is adequately torqued to specification and is backed up with
safety wire to hold it in place in the event that something should cause
the torque value to fall off.
Again, thanks for the ideas and support.
.
#18
Le Mans Master


Member Since: Feb 2000
Location: Bedford NH
Posts: 5,708
Likes: 0
Received 1 Like
on
1 Post
Cruise-In II Veteran


Well, to find the proper torque for a given fastener, you could measure the torque to failure outside of the part and go 70% that value. Can you use a stud and custom barrel nut like this:
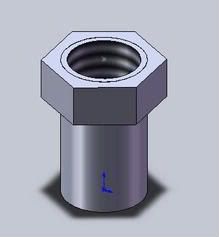
I will send you the drawing to get it made if you wish. The thread is an M6 (or whatever you need) and the hex is 10mm. I can make the model reflect whatever is necessary.
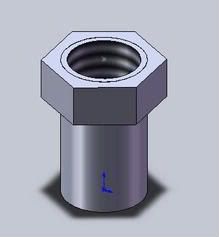
I will send you the drawing to get it made if you wish. The thread is an M6 (or whatever you need) and the hex is 10mm. I can make the model reflect whatever is necessary.
Last edited by ghoffman; 06-10-2008 at 08:15 PM.