Proper design and routing for crankcase evacuation
#21
Melting Slicks


Thread Starter

Cool. Do you have a checkvalve inline to prevent boost from entering the crankcase through the IM? Some evacuation is far better then none for sure, but as some boost is being generated at anything but an idle, that intake manifold vacuum quickly becomes non existent as far as ability to evacuate.

#22
Race Director


Member Since: May 2004
Location: Raleigh, NC
Posts: 16,664
Received 1,194 Likes
on
1,053 Posts
St. Jude Donor '15


Yep. It uses basically a supra PCV valve if I remember correctly.
That setup is long gone on mine.. I didn't care for it.. but wanted to at least put that out there so everyone that is running that setup doesn't totally freak out and think their engine is going to melt from acids overnight
But.. there are better options than that setup for sure, no argument there.
That setup is long gone on mine.. I didn't care for it.. but wanted to at least put that out there so everyone that is running that setup doesn't totally freak out and think their engine is going to melt from acids overnight

But.. there are better options than that setup for sure, no argument there.
#23
Melting Slicks


Thread Starter

Yes, there is no "overnight" engine failure, in fact most will not see the accelerated wear to the point of excessive oil consumption and related symptoms until 40-50k miles with the little evacuation that does take place. So it is not a reason to ever panic, but should be addressed with a proper evacuation system. Todays oils and materials used in the engine components are far superior to the old days of pre-1960's when all engines had similar venting (draft tube) systems. Those engine rarely went more than 40-50k miles before needing a rebuild as all of the contaminates causing wear were left in the crankcase. In the years following the mandate of the PCV system, these same engines, running the same oils began to last 2-3 times as long as prior to evacuation as an example. None of this occurs over night, and that is the reason so few understand what is occurring inside their engine. All engine oils have a TBN factor that is part of the ability to combat the sulfuric acid, and an in depth oil analysis shows all of this (not a base BlackStone, etc.).
Good contributions, and thanks!
Good contributions, and thanks!

#24
Melting Slicks


Thread Starter

Anyone else needing guidance, just post your questions!
#25

Does it make a difference taking the line from the inlet of the blower and moving it to the discharge? Right now on my A&A kit the line is in the filter on the blower but with the velocity stack with no filter I have no room for it without maybe drilling & tapping the stack/inlet which I'd rather not do. So would moving the line into the plumbing on the exit would it still create that suction or would it blow through the line?
#26
Race Director


Member Since: May 2004
Location: Raleigh, NC
Posts: 16,664
Received 1,194 Likes
on
1,053 Posts
St. Jude Donor '15


Vacuum vs. boost. Yeah, big difference.
The following users liked this post:
COSPEED2 (08-24-2016)
#27
Melting Slicks


Thread Starter

Correct.
Thanks schpenxel!
The key all of these kits need to improve is constant evacuation AND that the cleanside is always filtered and if possible MAF metered incoming air. Look close at the 3 diagrams from Turbonetics. They did extensive work on this and a centrifugal SC is basically the same in every way as a turbo except how the unit is driven. You can source all or any portion of the systems from Colorado Speed from the proper billet checkvalves to the cleanside alone, etc.
Let us know if we can help further!
Thanks schpenxel!
The key all of these kits need to improve is constant evacuation AND that the cleanside is always filtered and if possible MAF metered incoming air. Look close at the 3 diagrams from Turbonetics. They did extensive work on this and a centrifugal SC is basically the same in every way as a turbo except how the unit is driven. You can source all or any portion of the systems from Colorado Speed from the proper billet checkvalves to the cleanside alone, etc.
Let us know if we can help further!
#28

That setup actually still has the valley cover connected to the post TB vacuum source, so it's not as bad as you're making it out to be. It's still pulling some of the nasties out. The oil fill spout is basically open for for fresh air in under normal operation and can vent while in boost.
Not saying it's ideal, but isn't as bad as a full blown "stick a vented cap on it and remove everything else" setup like some people run
Not saying it's ideal, but isn't as bad as a full blown "stick a vented cap on it and remove everything else" setup like some people run
Under load on the dyno you can see haze coming out of the filter, not much, it's not a huge pressurized wind gust, but enough to carry oil with it and eventually saturate the filter.
#29

The venting you describe also retains ALL of the damaging combustion by-products and other contaminates that constantly enter as blow-by. An oil analysis will show how harmful this is to the engine over time.
Use the same system as shown in the Turbonetics diagrams as a centrifugal SC is the same as a turbo, only a belt drives the turbine instead of exhaust gasses. AT your power, you want the Monster CoSpeed system with cleanside unit. Or the Elite Ultra system w/cleanside. These systems are proven to properly evacuate in boosted power in excess of 1000 WHP, and also evacuate at all times, never allowing pressure to build and then seek to vent as you describe. This removes these contaminates as soon as they enter and are still in suspension before they can settle and mix with the engine oil. Once in the oil, most is there to stay as the oil filter only traps down to on average 15 microns in abrasive particulate size. 70% plus of all engine wear is from particles smaller than 15 microns. And the water and un-burnt fuel your retaining contaminating and diluting the oil know overwhelms the engine oils ability to protect.
Next best thing to a vacuum pump. You NEVER want to allow pressure to remain present and vent, that creates unstable piston rings and contributes to wear as well as the parasitic power loss of the pistons fighting pressure on the down stroke. Pull suction on the crankcase at all times.
The header collector evacuation systems work great, but only if you have no exhaust or mufflers. Otherwise the pressure pulses will rupture the venturi checkvalve diaphragm inside these. So no good for the street, but great for open headers as a "poor mans" vacuum pump.
Use the same system as shown in the Turbonetics diagrams as a centrifugal SC is the same as a turbo, only a belt drives the turbine instead of exhaust gasses. AT your power, you want the Monster CoSpeed system with cleanside unit. Or the Elite Ultra system w/cleanside. These systems are proven to properly evacuate in boosted power in excess of 1000 WHP, and also evacuate at all times, never allowing pressure to build and then seek to vent as you describe. This removes these contaminates as soon as they enter and are still in suspension before they can settle and mix with the engine oil. Once in the oil, most is there to stay as the oil filter only traps down to on average 15 microns in abrasive particulate size. 70% plus of all engine wear is from particles smaller than 15 microns. And the water and un-burnt fuel your retaining contaminating and diluting the oil know overwhelms the engine oils ability to protect.
Next best thing to a vacuum pump. You NEVER want to allow pressure to remain present and vent, that creates unstable piston rings and contributes to wear as well as the parasitic power loss of the pistons fighting pressure on the down stroke. Pull suction on the crankcase at all times.

The header collector evacuation systems work great, but only if you have no exhaust or mufflers. Otherwise the pressure pulses will rupture the venturi checkvalve diaphragm inside these. So no good for the street, but great for open headers as a "poor mans" vacuum pump.
#30
Melting Slicks


Thread Starter

The one change I made to mine is get rid of the OEM oil cap with screwed in filter to one that's clean-able and bigger on a billet cap. Also T-ed the line from the airfilter to both valve covers and retained the small glass catch can in between the valley and TB.
Under load on the dyno you can see haze coming out of the filter, not much, it's not a huge pressurized wind gust, but enough to carry oil with it and eventually saturate the filter.
https://www.youtube.com/watch?v=h0aE5U2ioFI
Under load on the dyno you can see haze coming out of the filter, not much, it's not a huge pressurized wind gust, but enough to carry oil with it and eventually saturate the filter.
https://www.youtube.com/watch?v=h0aE5U2ioFI
Read this to understand what I am describing. Venting has not been used professionally since the 60's and 70's. This is one of the most common misunderstandings I see more and more of today. There is no negative to proper evacuation and pulling suction at all times on an engine, and tons to defeat the PCV systems functions and vent:
http://www.dragzine.com/tech-stories...en-horsepower/
These are not "catch-cans" as most are as that is a misnomer assigned to all air/oil separation devices, these are true air/oil separating crankcase evacuation systems.
They give all the advantages a belt driven vacuum pump does, but for street use closed emissions compliant design. (NOT CARB approved for CA), and if the special Venturi valve is used, you can also add an adjustable vacuum relif valve on the fresh/cleanside valve cover and maintain steady vacuum for added power gains.
Here are the diagrams from Turbonetics that go over all of how these work on a LS based engine, LT based the foul and fresh sides are reversed:
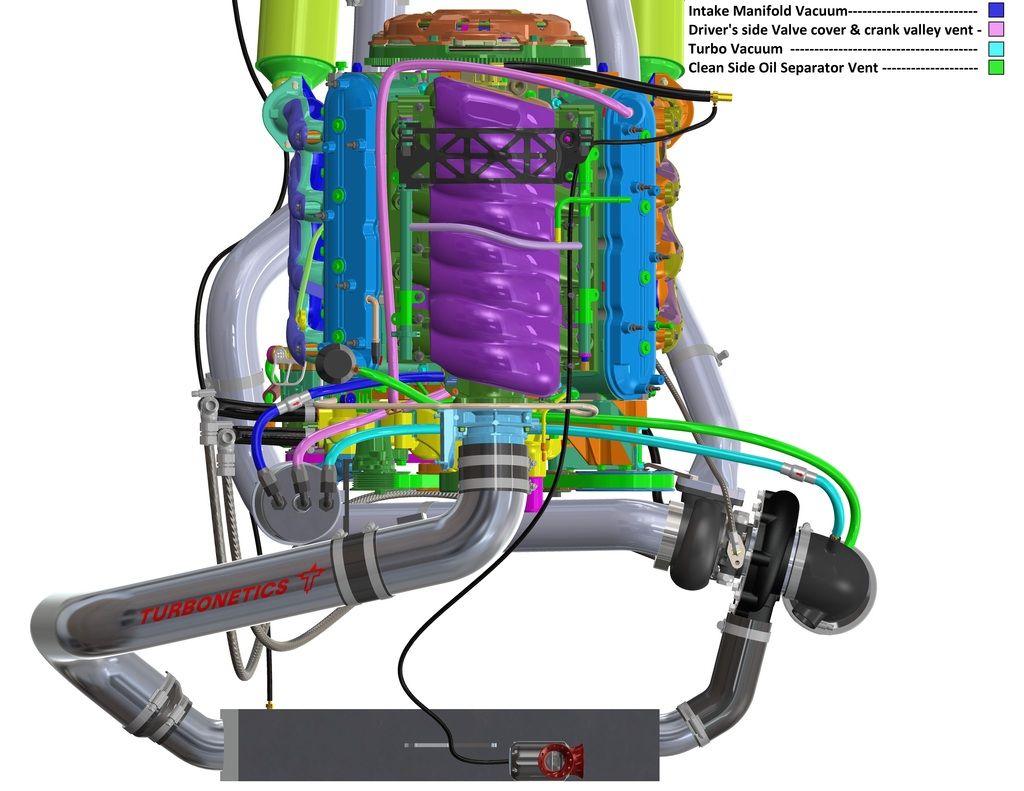
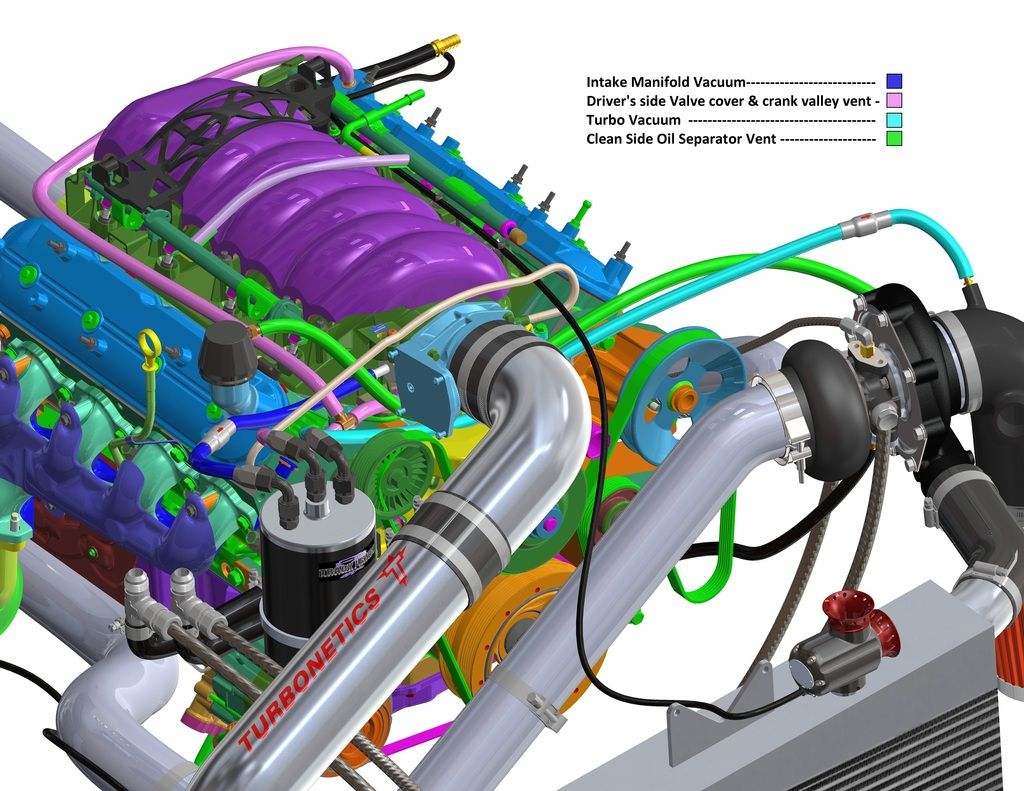
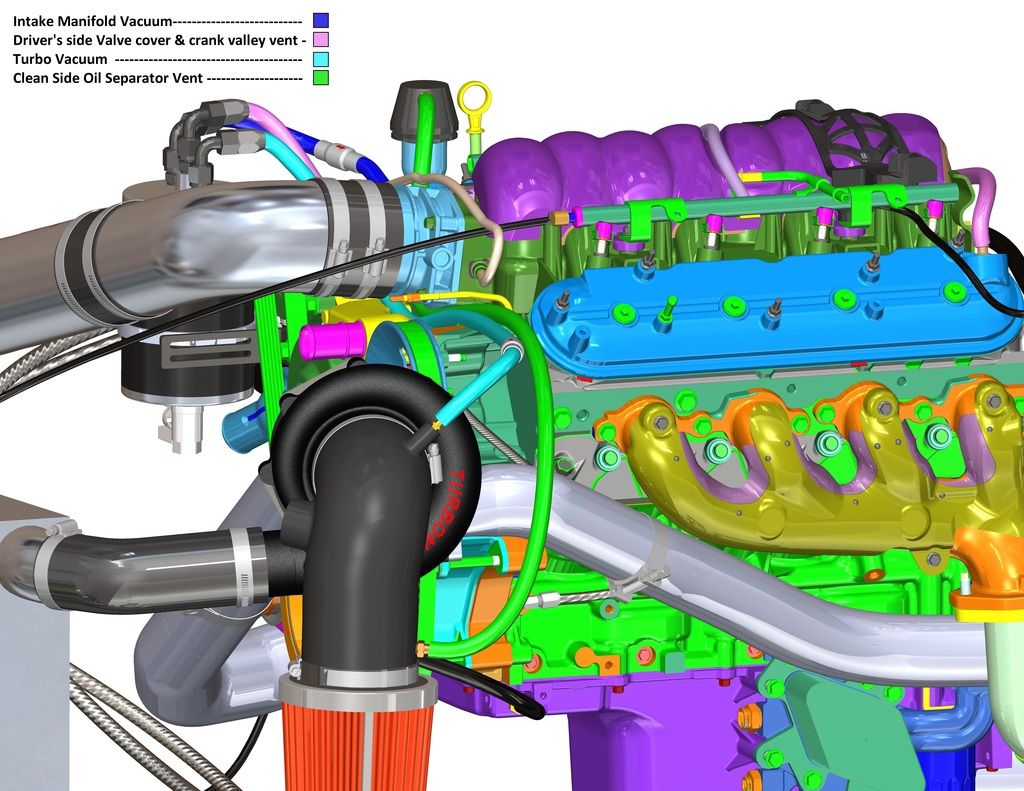
The special Venturi valve for Turbo and Centri blowers is well under $100 as well, so very affordable.
These systems stop 95% plus of the oil most and other contaminate ingestion to the intake air charge, enhance crankcase evacuation to be present at all modes of running, prevent any pressure from building, keep engine oil far cleaner retaining viscosity levels and removing un burnt fuel and water dilution, and reduce knock retard allowing a more accurate tune.
Over time, they reduce internal wear and varnish and carbon deposits on the rings and in the ring grooves.
Research and study proper crankcase evacuation and how vacuum pumps and proper crankcase evacuation aid in both power and engine longevity.
On all of our Professional race cars, (Top Dragster, Super Comp, Super Gas, and Comp) we run belt driven vacuum pumps as most all competitors do also. And as vacuum pumps will not last long in street use (a few thousand miles max before vanes need replaced, bearings, shafts & seals wear out, etc.) so these are the next best thing, and if the Venturi valve and vacuum relief valve is used, you duplicate all of the functions of the vacuum pump.
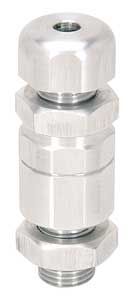
This allows you to install this on the fresh/cleanside of the crankcase and adjust it to maintain a target 14-15" of vacuum at all times (you do not want to pull more or oil begins to be pulled from wrist pins, etc. causing galling and damage). You can put a vacuum gauge tapped into a valve cover to see the vacuum present and no pressure ever builds, unless you have piston/ring/cylinder wall sealing issues or damage, or a leaking gasket.
It is so easy to ignore what you cannot see occurring, but the PCV system is why engines started to last 100-150k miles when they were mandated in the mid 1960's as before they only lasted 40-50k miles before needing a rebuild, and that was the same engines and same oils and oil change intervals back then. NOTHING else changed!
So when someone deletes the PCV systems functions, and allows all of the contaminates to settle and mix with the engine oil, the oil cannot maintain the protection need as it is overwhelmed with contaminates. And your oil filter will only trap down to 10-15 microns for the better filters. 70% plus of all internal engine wear is caused by particles smaller than the filter can trap, and the filter does nothing to remove the un-burnt fuel, water, and acid entering. Only the abrasive particulate matter. Far too many just think "pressure" and want to vent it. Read simple flow dynamic principles and see that to vent, pressure will always be greater on the side it is venting from to be able to force out to equalize. That is why you want suction pulled at all times.
#31
Melting Slicks


Thread Starter

Moving this up to keep it in view.
#32
Melting Slicks


Thread Starter

Have these systems in stock all!!!!
#33
Melting Slicks


Thread Starter

Bumping up for more discussion!
#34
Melting Slicks



So how would you run the lines on a N/A application in say a Z06 dry sump? Do you have to run the vacume to the tank? Above it says to block off all the pcv lines, on a z the lines go to the dry sump tank? Do you put the dry sump tank on its own circuit?
#35
Melting Slicks


Member Since: Nov 2009
Location: Klein TX
Posts: 3,038
Received 906 Likes
on
570 Posts
2023 C6 of the Year Finalist - Unmodified
2022 C6 of the Year Finalist - Unmodified


Sorry, I still don't understand how you can use one volume of air as a fresh air source and a vacuum source at the same time. Am I missing something, or just dumb?
#36
Melting Slicks


Thread Starter

The instructions for the dry sump are as follows:
Disconnect the front most barb on the oil reservoir and snap it onto the CSS that replaces the factory oil fill cap. This now changes the incoming fresh/clean air so it cannot easily "burp" oil into the main intake air bridge assy.
Run a hose from the front most barb now left open to a T you install into the hard plastic line from the sump tank to the valve covers. That covers the clean, or fresh side.
Now the can itself will run the center fitting to the valley cover of the engine (underneath the TB). One outer fitting from can with checkvalve flowing away from the can will connect to the vacuum barb that originally had a U shaped line connecting it to the valley. This provides vacuum for evacuation when at idle, cruise, and deceleration to remove the foul damaging compound laden vapors from the crankcase that the clean/fresh air is flushing and replacing. The second outlet on can w/valve flowing away from the can now connects to a barb you install into the coupler that attaches the main intake air tube to the throttle body. The reversion pules that cancel the intake manifolds vacuum when accelerating or at WOT will not reach past the TB until well over 8k RPM's, so this area will produce good strong suction to continue evacuation during periods of acceleration and WOT to continue constant evacuation preventing pressure from ever building during these periods where when stock, or with an average catchcan, as the checkvalves will automatically default to use the strongest suction source present at any given time providing full time evacuation. No pressure can have the chance to build, most all of the contaminates constantly entering as blow-by that would normally settle and mix with the engine oil contributing to wear of the engines internals, and as you are preventing pressure from building, piston rings retain stability resulting in less blow-by, and all around substantial improvement of power, engine life, etc.
wjnjr. Not sure I am following your question.
All PCV systems whether a OEM stock, or an aftermarket vacuum pump system have 2 main parts. The clean, or fresh side that provides filtered fresh and MAF metered (if not speed density) incoming air that enters one bank or portion of the crankcase, that flushes and makes up for the foul/dirty contaminate laden vapors being evacuated (sucked out) the opposite bank or portion of the crankcase (as in a L4 or L6 engine configuration).
As all OEM PCV systems rely solely on the intake manifold, this vacuum used is only present at idle, cruise, and deceleration (turbo or centri blower really only at idle and deceleration) so during these periods of acceleration, no evacuation takes place and crankcase pressure builds as well as the constantly entering combustion by-products are bringing in water, unburnt fuel, sulfuric acid, and abrasive soot/ash/carbon particles. If these are not flushed and removed from the crankcase as soon as they enter before they have a chance to settle, they quickly settle and mix with the engine oil, and that is where most wear comes from. These contaminates are what overwhelm the engine oils ability to protect, and as app 70% of all internal engine wear is caused by particles smaller than the 15 microns the average oil filter can trap down to, they are there to stay and constantly circulate through the engine causing wear. When accelerating or at WOT the cam lobe overlap allows reversion pulses to travel backwards up the intake runners canceling any usable vacuum (even though a tremendous volume of incoming air charge is present, no vacuum is present) so this is the period when pressure builds in the crankcase. The dual outlets and dual suction sources used with these systems provide full time evacuation. Oil stays cleaner longer, oil mist and other contaminates that reduce the efficiency of the combustion process and cause detonation are removed allowing only clean scrubbed incoming air charge. Less KR means more power and better fuel economy as the engine can run at optimum efficiency.
If your asking about pulling and maintaining a certain amount of vacuum, that requires a vacuum relief valve be installed in the opposite valve cover that your evacuating from so that once a set amount of vacuum is reached, the valve begins to allow in the fresh/clean side air. It is important if doing so, to keep vacuum at no more than 14-15" or oil begins to be pulled from the wrist pins. A belt driven vacuum pump is the most effective way to accomplish this, but they are not practical for street use as they wear rapidly and require replacement of vanes, seals, bearings, and quite often the main shaft every few thousand miles. We use them on all of our race engines just as every professional race class uses.
Let me know if that answered your question, if not, please go into more detail.
Disconnect the front most barb on the oil reservoir and snap it onto the CSS that replaces the factory oil fill cap. This now changes the incoming fresh/clean air so it cannot easily "burp" oil into the main intake air bridge assy.
Run a hose from the front most barb now left open to a T you install into the hard plastic line from the sump tank to the valve covers. That covers the clean, or fresh side.
Now the can itself will run the center fitting to the valley cover of the engine (underneath the TB). One outer fitting from can with checkvalve flowing away from the can will connect to the vacuum barb that originally had a U shaped line connecting it to the valley. This provides vacuum for evacuation when at idle, cruise, and deceleration to remove the foul damaging compound laden vapors from the crankcase that the clean/fresh air is flushing and replacing. The second outlet on can w/valve flowing away from the can now connects to a barb you install into the coupler that attaches the main intake air tube to the throttle body. The reversion pules that cancel the intake manifolds vacuum when accelerating or at WOT will not reach past the TB until well over 8k RPM's, so this area will produce good strong suction to continue evacuation during periods of acceleration and WOT to continue constant evacuation preventing pressure from ever building during these periods where when stock, or with an average catchcan, as the checkvalves will automatically default to use the strongest suction source present at any given time providing full time evacuation. No pressure can have the chance to build, most all of the contaminates constantly entering as blow-by that would normally settle and mix with the engine oil contributing to wear of the engines internals, and as you are preventing pressure from building, piston rings retain stability resulting in less blow-by, and all around substantial improvement of power, engine life, etc.
wjnjr. Not sure I am following your question.
All PCV systems whether a OEM stock, or an aftermarket vacuum pump system have 2 main parts. The clean, or fresh side that provides filtered fresh and MAF metered (if not speed density) incoming air that enters one bank or portion of the crankcase, that flushes and makes up for the foul/dirty contaminate laden vapors being evacuated (sucked out) the opposite bank or portion of the crankcase (as in a L4 or L6 engine configuration).
As all OEM PCV systems rely solely on the intake manifold, this vacuum used is only present at idle, cruise, and deceleration (turbo or centri blower really only at idle and deceleration) so during these periods of acceleration, no evacuation takes place and crankcase pressure builds as well as the constantly entering combustion by-products are bringing in water, unburnt fuel, sulfuric acid, and abrasive soot/ash/carbon particles. If these are not flushed and removed from the crankcase as soon as they enter before they have a chance to settle, they quickly settle and mix with the engine oil, and that is where most wear comes from. These contaminates are what overwhelm the engine oils ability to protect, and as app 70% of all internal engine wear is caused by particles smaller than the 15 microns the average oil filter can trap down to, they are there to stay and constantly circulate through the engine causing wear. When accelerating or at WOT the cam lobe overlap allows reversion pulses to travel backwards up the intake runners canceling any usable vacuum (even though a tremendous volume of incoming air charge is present, no vacuum is present) so this is the period when pressure builds in the crankcase. The dual outlets and dual suction sources used with these systems provide full time evacuation. Oil stays cleaner longer, oil mist and other contaminates that reduce the efficiency of the combustion process and cause detonation are removed allowing only clean scrubbed incoming air charge. Less KR means more power and better fuel economy as the engine can run at optimum efficiency.
If your asking about pulling and maintaining a certain amount of vacuum, that requires a vacuum relief valve be installed in the opposite valve cover that your evacuating from so that once a set amount of vacuum is reached, the valve begins to allow in the fresh/clean side air. It is important if doing so, to keep vacuum at no more than 14-15" or oil begins to be pulled from the wrist pins. A belt driven vacuum pump is the most effective way to accomplish this, but they are not practical for street use as they wear rapidly and require replacement of vanes, seals, bearings, and quite often the main shaft every few thousand miles. We use them on all of our race engines just as every professional race class uses.
Let me know if that answered your question, if not, please go into more detail.
