Catch can options
#21
Melting Slicks



Pressure on a gauge with respect to moving air molecules through an air pump, is a measure of restriction. Boost is a measure of restriction in the intake air pathway. Vacuum is a measure of restriction in the air intake pathway. Neither one can occur without some kind of 'obstacle' to flow. For an example if you install a very restrictive air filter, or put your hand over the air intake tube to block it completely, you will have a vacuum in the tube when the engine or supercharger or turbo (any air pump) attempts to draw on air molecules present there and none are replenished. Without the restriction of your hand or a tiny air filter, there is no vacuum, the pressure is absolutely absolute (atmospheric absolute).
To think of this another way. Imagine air molecules are things, like baseballs. Tiny but physical and very real. An engine can 'move' air molecules around, imagine an engine is a 'scoop' that simply scoops up air molecules (baseballs) and moves them into another chamber. This analogy works for superchargers too because they are also air pumps which scoop up baseballs and move them to another chamber.
So now imagine the engine or air pump is scooping baseballs out of a big cup or something. If you replace the baseballs as fast as you are taking them out, there won't ever be any baseball deficit (vacuum). The low pressure vacuum signal you get when air pumps scoop all the air out of a space and leave nothing behind is only possible when the source of the air molecules is cut off or somehow restricted. In the case of our atmosphere, there is no limit to the number of air molecules that can take the place of those which are scooped out, so there will never be any vacuum unless you specifically restrict incoming air somehow (i.e. tiny or filthy air filter, restrictor plates, etc)
To think of this another way. Imagine air molecules are things, like baseballs. Tiny but physical and very real. An engine can 'move' air molecules around, imagine an engine is a 'scoop' that simply scoops up air molecules (baseballs) and moves them into another chamber. This analogy works for superchargers too because they are also air pumps which scoop up baseballs and move them to another chamber.
So now imagine the engine or air pump is scooping baseballs out of a big cup or something. If you replace the baseballs as fast as you are taking them out, there won't ever be any baseball deficit (vacuum). The low pressure vacuum signal you get when air pumps scoop all the air out of a space and leave nothing behind is only possible when the source of the air molecules is cut off or somehow restricted. In the case of our atmosphere, there is no limit to the number of air molecules that can take the place of those which are scooped out, so there will never be any vacuum unless you specifically restrict incoming air somehow (i.e. tiny or filthy air filter, restrictor plates, etc)
#22
Burning Brakes



Well I assure you that the atmosphere is always atmospheric. Think about the air filter, what drives air into the filter? It isn't the supercharger- its the atmospheric pressure.
compressor of turbocharger = compressor of supercharger. Both units do the same thing. One is driven by a belt, one by exhaust gas. End result is the same.
Imagine you remove the filter from a running engine. What is the pressure in front of the throttle body or compressor? atmospheric. Now, run the engine at Idle, cruise, WOT, etc... What is the pressure in front of the throttle body/compressor? Still atmospheric. There is NEVER any vacuum in that region unless you specifically design the filter to be restrictive, which would reduce engine power.
compressor of turbocharger = compressor of supercharger. Both units do the same thing. One is driven by a belt, one by exhaust gas. End result is the same.
Imagine you remove the filter from a running engine. What is the pressure in front of the throttle body or compressor? atmospheric. Now, run the engine at Idle, cruise, WOT, etc... What is the pressure in front of the throttle body/compressor? Still atmospheric. There is NEVER any vacuum in that region unless you specifically design the filter to be restrictive, which would reduce engine power.
How does a hair dryer work, what about a centrifugal fluid pump or how does a vacuum clean your floors. All of them create a differential pressure at the impeller. As long as the impeller is spinning there is going to be a differential pressure to make the air move.
#23
Melting Slicks



I have exam tomorrow so I can't make the reply I want yet but,
What we really have is something like the Laplace equation, fluid with a given density in a gravity field, that has boundary conditions and initial conditions for setting up a partial differential equation.
Because our example is a low-flow (cruise situation or idle) steady state (flow is not changing) and it follows conservation laws (energy, mass), the differential terms for velocity, pressure, and mass (dV, dM, dP) are = 0.
A tire for example, if we start removing air the tire will gradually deflate, there will be a dP/dt term because it follows conservation of mass. However if I make a second hole to put the air back into the tire on the other side as fast as I am taking it out, the dP/dt term will be zero even though there is a flow rate. In other words, our tire or engine can have a very high flow rate of airflow (in CFM or lb/min) without expressing any differential of pressure terms.
What we really have is something like the Laplace equation, fluid with a given density in a gravity field, that has boundary conditions and initial conditions for setting up a partial differential equation.
Because our example is a low-flow (cruise situation or idle) steady state (flow is not changing) and it follows conservation laws (energy, mass), the differential terms for velocity, pressure, and mass (dV, dM, dP) are = 0.
A tire for example, if we start removing air the tire will gradually deflate, there will be a dP/dt term because it follows conservation of mass. However if I make a second hole to put the air back into the tire on the other side as fast as I am taking it out, the dP/dt term will be zero even though there is a flow rate. In other words, our tire or engine can have a very high flow rate of airflow (in CFM or lb/min) without expressing any differential of pressure terms.
#24
Burning Brakes



I have exam tomorrow so I can't make the reply I want yet but,
What we really have is something like the Laplace equation, fluid with a given density in a gravity field, that has boundary conditions and initial conditions for setting up a partial differential equation.
Because our example is a low-flow (cruise situation or idle) steady state (flow is not changing) and it follows conservation laws (energy, mass), the differential terms for velocity, pressure, and mass (dV, dM, dP) are = 0.
A tire for example, if we start removing air the tire will gradually deflate, there will be a dP/dt term because it follows conservation of mass. However if I make a second hole to put the air back into the tire on the other side as fast as I am taking it out, the dP/dt term will be zero even though there is a flow rate. In other words, our tire or engine can have a very high flow rate of airflow (in CFM or lb/min) without expressing any differential of pressure terms.
What we really have is something like the Laplace equation, fluid with a given density in a gravity field, that has boundary conditions and initial conditions for setting up a partial differential equation.
Because our example is a low-flow (cruise situation or idle) steady state (flow is not changing) and it follows conservation laws (energy, mass), the differential terms for velocity, pressure, and mass (dV, dM, dP) are = 0.
A tire for example, if we start removing air the tire will gradually deflate, there will be a dP/dt term because it follows conservation of mass. However if I make a second hole to put the air back into the tire on the other side as fast as I am taking it out, the dP/dt term will be zero even though there is a flow rate. In other words, our tire or engine can have a very high flow rate of airflow (in CFM or lb/min) without expressing any differential of pressure terms.
#25
Burning Brakes



I dont know why you're making this so hard lol
Just route it like how Mighty mouse shows, this is proven to work on hundred of thousands of cars. In fact I just emailed dave with my set up and he told me exactly how to route my system.
Just route it like how Mighty mouse shows, this is proven to work on hundred of thousands of cars. In fact I just emailed dave with my set up and he told me exactly how to route my system.
#26
Melting Slicks



So I am not sure it is possible to disagree given the insurmountable body of evidence
#27
Melting Slicks



You don't need to be familiar (experienced) with turbocharged setups to understand that.
Lets pick a number between 10 and 20" Hg, say 15" Hg cruise vacuum.
This should be extremely fundamental basic principles. If you have trouble at this point I recommend beginners books, guides, etc... to internal combustion
Next we convert 15" Hg to absolute pressure. This is also a basic setup, use an online calculator if necessary
15"Hg converted to absolute pressure is our atmospheric at sea level, 14.6959 minus the vacuum signal we remove in psi, 7.36731300858795 = 7.32psi
Finally, lets compare the absolute pressure in the atmosphere with the absolute pressure in the intake manifold.
14.69psi vs 7.32psi
Clearly the atmospheric pressure is higher. Since air will flow from regions of high pressure to low pressure, the air must be leaving the atmosphere and entering the crankcase, in order to reach the intake manifold.
#30
Melting Slicks



none of those (two) pictures will work because they show during intake manifold vacuum conditions the atmosphere is made available. I think you have the check valve reversed in the picture.
if the check valve is reversed then it lets pressure escape, and keeps air from entering the can.
I don't like the one where they are tied together. As I said above, this forces the checkvalve operation to clear blow-by during boost situations which adds an unwanted point of potential failure.
Next the other problem is the additional volume created by additional lines/can. During boost, the can acts as an additional crankcase volume reservoir which undermines (reduces the effectiveness of) the PCV operation.
if the check valve is reversed then it lets pressure escape, and keeps air from entering the can.
I don't like the one where they are tied together. As I said above, this forces the checkvalve operation to clear blow-by during boost situations which adds an unwanted point of potential failure.
Next the other problem is the additional volume created by additional lines/can. During boost, the can acts as an additional crankcase volume reservoir which undermines (reduces the effectiveness of) the PCV operation.
#32
Melting Slicks



You can eliminate the breather and the check valve on the catch can. That way the entire crankcase volume contents will flow towards the atmospheric pressure behind the air filter.
If you left the check valve/breather there, it wouldn't do anything unless the engine produced an excessive amount of blow-by during WOT, in which case the engine is likely blown and needs a rebuild.
In other words, the pcv vacuum resource during WOT isn't the intake manifold- Its the post air filter tube. That is where pressure will be at atmospheric or lower (if the filter is restrictive the pressure after it will be lower than atmospheric).
If you left the check valve/breather there, it wouldn't do anything unless the engine produced an excessive amount of blow-by during WOT, in which case the engine is likely blown and needs a rebuild.
In other words, the pcv vacuum resource during WOT isn't the intake manifold- Its the post air filter tube. That is where pressure will be at atmospheric or lower (if the filter is restrictive the pressure after it will be lower than atmospheric).
#34
Melting Slicks



Another couple issues potentially
1. is the check valve you are using rated for 250*F~ oil and gasoline use
2. if the check valve between intake manifold and crankcase flow is significant it poses a threat to the oil seals of the engine.
In other words, PCV check valves should be flow-limiting for the application. V8 engine size crankcases need more PCV flow than small 4-cylinder engine crankcases. So the pcv valve has to flow enough to meet the demands of the crankcase, but not so much that it pulls the crankcase down below 2-4" Hg where it will both pull against the wet sump oil pump (less oil system flow) and it can also damage an oil seal (the engine's oil seals such as front and rear main seals are not designed for significant vacuum or pressure, and will leak or become damaged if there is excess pressure in either direction)
Setting up a custom crankcase is simple but if you ignore the setting up part and just tie a bunch of parts together it might not work well, or it might work too well. The PCV system is a TUNED system where the owner must specifically set the crankcase flow manually if they are setting it up manually. By using OEM pcv valves and OEM hoses/tubes you are using the factory's set up. If you change say the check valve (pcv valve) and now it flows double or triple what the OEM pcv valve flows, you have a major issue that can damage the engine. Even though it still 'functions' and seems to work normally. You wouldn't be able to tell without putting a gauge on the crankcase. Which ironically is how you set the flow to begin with (install gauge -> modify orifice diameter at check valve and fresh air filtered vent to achieve desired pressure)
Typically you want a very small hole on the check valve so that the consequences of a blocked or damaged fresh air vent are minimized.
To set crankcase pressure, adjust mostly the orifice diameter at the fresh air vent, erring on the large side to account for future crust/carbon buildup/hose clogging contents/etc...
OEM crankcase fresh air vent tubes often have restrictors in them for this purpose (would you like a picture of one)
1. is the check valve you are using rated for 250*F~ oil and gasoline use
2. if the check valve between intake manifold and crankcase flow is significant it poses a threat to the oil seals of the engine.
In other words, PCV check valves should be flow-limiting for the application. V8 engine size crankcases need more PCV flow than small 4-cylinder engine crankcases. So the pcv valve has to flow enough to meet the demands of the crankcase, but not so much that it pulls the crankcase down below 2-4" Hg where it will both pull against the wet sump oil pump (less oil system flow) and it can also damage an oil seal (the engine's oil seals such as front and rear main seals are not designed for significant vacuum or pressure, and will leak or become damaged if there is excess pressure in either direction)
Setting up a custom crankcase is simple but if you ignore the setting up part and just tie a bunch of parts together it might not work well, or it might work too well. The PCV system is a TUNED system where the owner must specifically set the crankcase flow manually if they are setting it up manually. By using OEM pcv valves and OEM hoses/tubes you are using the factory's set up. If you change say the check valve (pcv valve) and now it flows double or triple what the OEM pcv valve flows, you have a major issue that can damage the engine. Even though it still 'functions' and seems to work normally. You wouldn't be able to tell without putting a gauge on the crankcase. Which ironically is how you set the flow to begin with (install gauge -> modify orifice diameter at check valve and fresh air filtered vent to achieve desired pressure)
Typically you want a very small hole on the check valve so that the consequences of a blocked or damaged fresh air vent are minimized.
To set crankcase pressure, adjust mostly the orifice diameter at the fresh air vent, erring on the large side to account for future crust/carbon buildup/hose clogging contents/etc...
OEM crankcase fresh air vent tubes often have restrictors in them for this purpose (would you like a picture of one)
Last edited by Kingtal0n; 03-28-2019 at 05:45 PM.
#35
Melting Slicks



I just looked at (one) of the routes and its true that they have an additional check valve on the can with a breather. Which I think is strange since the air is leaving the crankcase, why filter it? At first I don't know why the filter is there. And then I realize that of course you can't have any kind of entrance or exit without a filter.
So why the check valve though? maybe the engine crankcase doesn't flow well from left to right for some reason and having the additional breather port is a nice addition to that SIDE of the engine. (now theres two exits instead of just one). Its like enlarging the fresh air vent but only for positive crankcase pressure situations, i.e. it does not contribute to crankcase idle/cruise flow. Its just an easy door to push open in the event that crankcase pressure is rising too quickly- again suggestive of a blown engine. But maybe the owner wants to keep driving even with the blow-by. Maybe the engine is hurt or extremely worn out, but the owner wants to keep drving it. These are the conditions where having this sort of additional blow-by relief, oil catch canister would be ideal. So there are practical uses for devices of this nature. It is simple and it provides the engine with a proper bandaid if you are using a bandaid device. It just isn't sensible or desirable to show this sort of thing off for healthy, normally low-blow by daily driver applications to have this sort of additional unwanted component hogging up volume of the crankcase in the engine bay (adding volume to the crankcase and putting it external in the engine bay) unless you actually needed it to catch oil and relief pressure in excess. Or, some people just like the way they look. I knew plenty of folks that just wanted the thing in there, shiny. It wouldn't hurt anything to just have it anyways (it always "works")
Since the crankcase is attached to the (compressor inlet or pre-throttle body tube) that is the direction you want crankcase gas to flow during WOT. There won't be any benefit for (self) crankcase evacuation (that is what we are trying to avoid by using PCV in the first place). If you had a vacuum pump you would send it there instead. In either case, vacuum pump or post air filter tube, the same idea applied: low pressure signal pulls on the crankcase. (As opposed to letting it push itself out through some kind of check valve).
letting blowby build up to the point that it can push past any 1-way check valve on the catch can means that we have already failed in our duty to reduce crankcase pressure (the definition of PCV). i.e. the crankcase pressure should start out below atmospheric, and stay that way for the entire run. If this is done properly (PCV action) it would never open a check valve designed to relief pressure to the atmosphere (because it will be trying to suck the atmosphere into the crankcase against the check valve)
So why the check valve though? maybe the engine crankcase doesn't flow well from left to right for some reason and having the additional breather port is a nice addition to that SIDE of the engine. (now theres two exits instead of just one). Its like enlarging the fresh air vent but only for positive crankcase pressure situations, i.e. it does not contribute to crankcase idle/cruise flow. Its just an easy door to push open in the event that crankcase pressure is rising too quickly- again suggestive of a blown engine. But maybe the owner wants to keep driving even with the blow-by. Maybe the engine is hurt or extremely worn out, but the owner wants to keep drving it. These are the conditions where having this sort of additional blow-by relief, oil catch canister would be ideal. So there are practical uses for devices of this nature. It is simple and it provides the engine with a proper bandaid if you are using a bandaid device. It just isn't sensible or desirable to show this sort of thing off for healthy, normally low-blow by daily driver applications to have this sort of additional unwanted component hogging up volume of the crankcase in the engine bay (adding volume to the crankcase and putting it external in the engine bay) unless you actually needed it to catch oil and relief pressure in excess. Or, some people just like the way they look. I knew plenty of folks that just wanted the thing in there, shiny. It wouldn't hurt anything to just have it anyways (it always "works")
Since the crankcase is attached to the (compressor inlet or pre-throttle body tube) that is the direction you want crankcase gas to flow during WOT. There won't be any benefit for (self) crankcase evacuation (that is what we are trying to avoid by using PCV in the first place). If you had a vacuum pump you would send it there instead. In either case, vacuum pump or post air filter tube, the same idea applied: low pressure signal pulls on the crankcase. (As opposed to letting it push itself out through some kind of check valve).
letting blowby build up to the point that it can push past any 1-way check valve on the catch can means that we have already failed in our duty to reduce crankcase pressure (the definition of PCV). i.e. the crankcase pressure should start out below atmospheric, and stay that way for the entire run. If this is done properly (PCV action) it would never open a check valve designed to relief pressure to the atmosphere (because it will be trying to suck the atmosphere into the crankcase against the check valve)
Last edited by Kingtal0n; 03-28-2019 at 06:25 PM.
#36

These are the specs of the valves
High temperature 160℃, acid, oil, ozone resistance;
Material: Plastic, silicone valve core
Diameter: 10mm
Total length: 58mm
Suitable gas, liquid
Opening Pressure: >0.015MPA
Aback pressure: <1MPA
High temperature 160℃, acid, oil, ozone resistance;
Material: Plastic, silicone valve core
Diameter: 10mm
Total length: 58mm
Suitable gas, liquid
Opening Pressure: >0.015MPA
Aback pressure: <1MPA
#37
Melting Slicks



PCV selection for high performance is indepth analysis and tuning of variables,
see for example
www.engineprofessional.com/articles/EPQ315_34-44.pdf
So you see, letting the crankcase pressure build and push open a check valve means the PCV system is NOT working properly.
see for example
www.engineprofessional.com/articles/EPQ315_34-44.pdf
We elected to use crankcase pressure as a metric for evaluating the PCV system’s
performance. Measurement with sensitive instrumentation confirmed what we already knew; if the PCV system is working properly, a slight vacuum should be present in the crankcase. This is not vacuum to the level of that which would be observed with a crankcase vacuum pump, however if the PCV valve is properly ventilating the crankcase, fresh air should be pulled in through the crankcase inlet breather or hose. To trigger this flow, a pressure differential must be present from the outside atmosphere to the inside of the crankcase. If the PCV system is not functioning properly, the crankcase will push vapors out of the crankcase
inlet vent or hose. In this condition, the crankcase will be under positive pressure.
performance. Measurement with sensitive instrumentation confirmed what we already knew; if the PCV system is working properly, a slight vacuum should be present in the crankcase. This is not vacuum to the level of that which would be observed with a crankcase vacuum pump, however if the PCV valve is properly ventilating the crankcase, fresh air should be pulled in through the crankcase inlet breather or hose. To trigger this flow, a pressure differential must be present from the outside atmosphere to the inside of the crankcase. If the PCV system is not functioning properly, the crankcase will push vapors out of the crankcase
inlet vent or hose. In this condition, the crankcase will be under positive pressure.
#38
Melting Slicks



Just to use my car as an example. Going by your first paragraph your saying that with my impeller spinning at 9000 rpm (engine idle speed of 1000 rpm) there is only atmospheric pressure inside the filter? There has to be a differential pressure for the air to move through the filter otherwise it would be stagnant.
How does a hair dryer work, what about a centrifugal fluid pump or how does a vacuum clean your floors. All of them create a differential pressure at the impeller. As long as the impeller is spinning there is going to be a differential pressure to make the air move.
How does a hair dryer work, what about a centrifugal fluid pump or how does a vacuum clean your floors. All of them create a differential pressure at the impeller. As long as the impeller is spinning there is going to be a differential pressure to make the air move.
When you say "differential pressure" in this context you are referring to the difference in pressure which causes flow. Which I have provided much earlier in the thread:
https://www.corvetteforum.com/forums...post1599116384
As to how it works in the above picture using numbers,
the intake section is approx 18" Hg, (14.5 - 9) = 5~psi absolute
the crankcase is approx 2 to 4" Hg of pressure, (10-12psi absolute)
the atmospheric vent tube (pre compressor) is approximately atmospheric pressure (14.45~psi)
the intake section is approx 18" Hg, (14.5 - 9) = 5~psi absolute
the crankcase is approx 2 to 4" Hg of pressure, (10-12psi absolute)
the atmospheric vent tube (pre compressor) is approximately atmospheric pressure (14.45~psi)
The term 'differential pressure' sounds to me like dP/dt, or change in pressure with respect to time. Which, dP/dt=0 for steady state when pressure isn't changing. "A steady state for a differential equation is a solution where the value of y does not change over time." faculty.cas.usf.edu/jkwilde/mathcamp/Differential_Equations.pdf
A way the term could be used and not be zero is to describe from the instantaneous conditions for when the system is at rest initially, and then it is turned on and run for some time. For example if the impeller of the turbo is at 0rpm, and then it begins to spin, what is the differential pressure? At first, t=0, at 0rpm, dP/dt=0. I suppose we could use dP/dt to model these conditions since the pressure changes gradually with time, however there are probably other more effective means of arriving at a solution. Maybe If we integrate dP/dt for t=0 to infinity we could get a solution for pressure after time went to infinity. The differential should increase and then either decrease to zero as the compressor flow taps out, and converge to some final value, otherwise the differential must go to infinity. And we know real world impellers don't change pressure to infinity so the solution must be a convergence to some number P, and dP/dt is gone. I don't think this is what we are interested in though, or what you meant by differential pressure. Pressure is a scalar, maybe we should describe a pressure gradient as "pressure is a function of both position and time"(pg97 fluid mechanics), and maybe I should have started with analyzing the problem first in this sense. I just wanted to be clear about our terminology and the word 'differential' means rate or rate of change and if you put it with something: "cat differential" it means rate of change of cat. so 'pressure differential' is rate of change of pressure. In a steady state, the pressure is held steady, there is no rate of change.
I am realizing how confusing this issue is. All over the internet it says dP is differential pressure as a difference between two points. For example,
https://www.nrc.gov/reading-rm/basic...-dp-or-dp.html
"The difference in pressure between two points of a system, such as between the inlet and outlet of a pump."
I pulled out the fluid mechanics book and I believe this is what I am recalling:
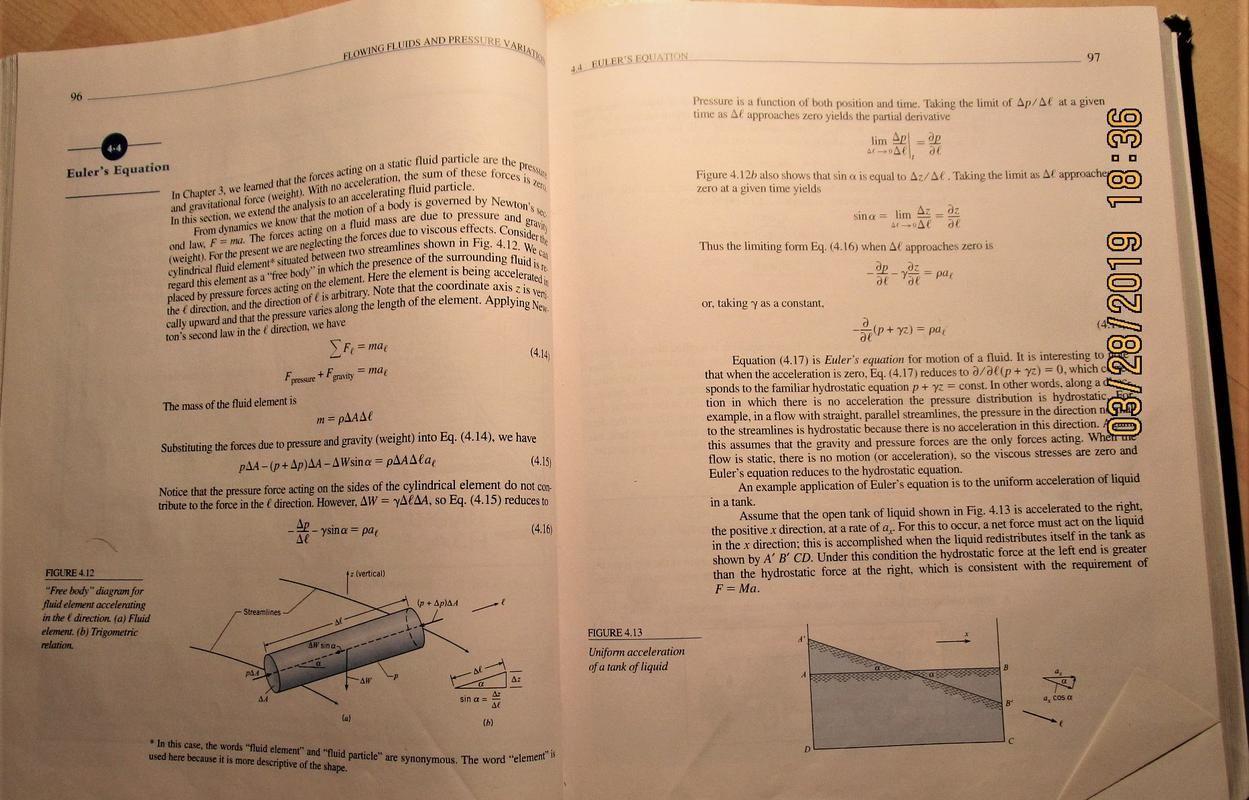
Allow me to read some of it here, in quotes,
"It is interesting to note that when the acceleration is zero, Euler's equation reduces to d(pressure+gamma*z)/dl = 0"
where gamma is density times gravity and z is fluid height (it is accounting for gravity in the vertical direction).
"In other words, along a direction in which there is no acceleration the pressure distribution is hydrostatic. "
Now, fluids is definetely not my strong suit. So who knows maybe I am not using it correctly.
I believe what this is saying is, if we take the differential pressure with respect to length of a pipe, because the conditions are steady state and there is no acceleration of fluid, there will be velocity terms but no dV/dt or dV/dl terms, the differential pressure is zero in Euler's equation.
So just to re-cap I've been taking the flow rate of PCV during steady state conditions as "uniform flow" where there are no local accelerations(pg. 93 are "due to unsteady flow") and no convective accelerations (where velocity is a function of position in a flow field) which of course sets acceleration to zero giving us zero for rate of change of pressure with respect to time and length
Last edited by Kingtal0n; 03-28-2019 at 08:58 PM.
The following users liked this post:
Irish31 (04-11-2019)
#40
Melting Slicks



The way its shown in the picture I provided is identical to the way you have it in your last drawing, minus of course the additional unwanted can portion. There is no can on factory healthy engines. When I see a can, I think blow-by, I think bad piston rings.