Do you use a "water wetter"?
#41
Le Mans Master



A fluid's volume doesn't change under pressure (appreciably on a macro scale) is true, but it doesn't mean it doesn't experience pressure. This is why it does not boil in a cooling system.
One thing I know is, if you take a fluid, put it under pressure and heat it passed it's non-pressurized boiling point , then release this pressure it will consume more heat (energy) to phase change to a gas. This is Latent Heat of Vaporization. Now, we are not doing this in our cooling system, but it is just an example of how playing with pressure/phase can effect behavior.
Really to do an apples to apples test, It would need to be under pressure in my opinion. IT would just be another variable that would remain having an unknown effect.
I am not sure of your test bench set up, but a cars cooling system is closed. Under pressure both sides of the pump should see pressure. The resistance out and the pressure pushing in should be relatively close in a closed system. The head resistance should still only be the flow losses. Again, I would have to have a look at what your set up is to fully understand.
One thing I know is, if you take a fluid, put it under pressure and heat it passed it's non-pressurized boiling point , then release this pressure it will consume more heat (energy) to phase change to a gas. This is Latent Heat of Vaporization. Now, we are not doing this in our cooling system, but it is just an example of how playing with pressure/phase can effect behavior.
Really to do an apples to apples test, It would need to be under pressure in my opinion. IT would just be another variable that would remain having an unknown effect.
I am not sure of your test bench set up, but a cars cooling system is closed. Under pressure both sides of the pump should see pressure. The resistance out and the pressure pushing in should be relatively close in a closed system. The head resistance should still only be the flow losses. Again, I would have to have a look at what your set up is to fully understand.
If you don't want me running it that way I'll think of something else I guess or just scrap the whole damn thing.
#42
Team Owner



Run it
#43
Team Owner


Pro Mechanic


#44
Melting Slicks



I use it most of the time in the C4s because they run hotter than my other vehicles. Water wetter or "hy-per lube super coolant" product. Nothing wrong with the cooling system, but I am willing to spend a few bucks to enhance the heat transfer for 4 years (between cooling system services).
#45
Drifting



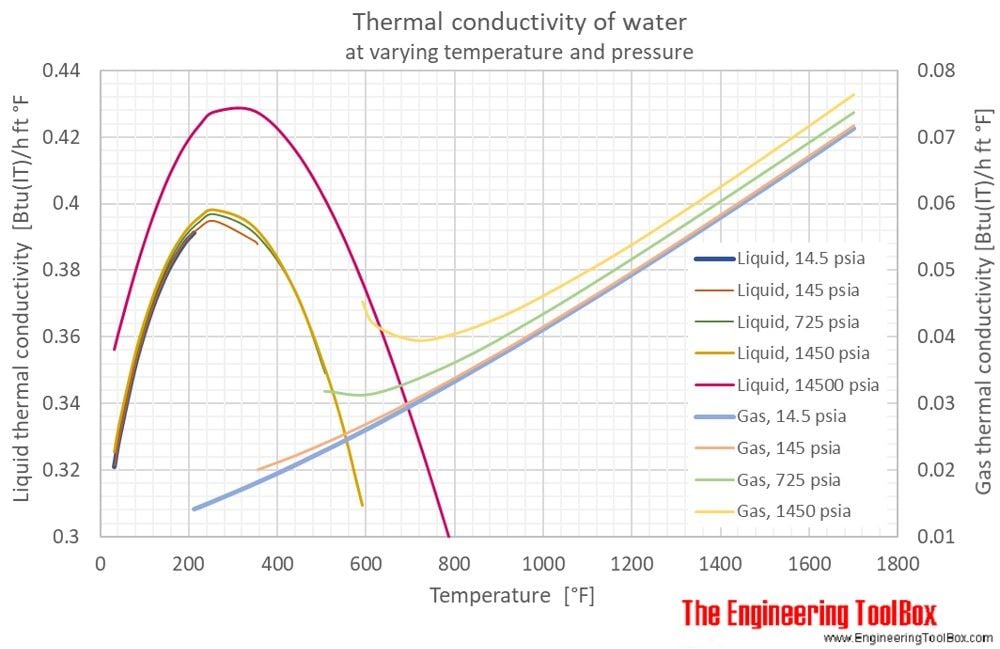
So, there is it. There is an interaction of both temperature and pressure. Although, it can clearly be seen here, it requires significant changes in pressure. The real question becomes does the addition of Water Wetter also affect the waters sensitivity to pressure as well. Pressure is working on the boundary layers of the fluid, which we believe the water wetter is also working on.
I think in the grand scheme of things, I agree with Tom, if it improves heat transfer in the absence of pressure, it will improve it under pressure and vice versa. The only thing we won't know is, is it the same improvement in thermal conductivity both with and without pressure and based off this chart, I would expect it to be so small it doesn't matter.
#46
Drifting



So with your test... you are going to heat it up, let it flow and record time to drop from and to a specific T. Seems reasonable and should produce a meaningful data point establishing the heat transfer coefficient. But the Temperature will not be the same across the entire system. Obviously it will be cooler exiting the heat exchanger than entering it. Maybe it is better to record the time to reach room temperature at the heat exchanger's entrance?
Let's consider this though: This isn't really what happens in our car's cooling system. The heat source heats a medium that the water is then transferred through (Our Block). The goal isn't necessarily to have cooler fluid it is to have a cooler engine. The point where the temperature reading is taken in a cooling system is also meaningful. Pre/Post heat exchanger, up or down stream of the heating source, etc. If in the time the fluid is in the engine, it can absorb and carry more heat, is a higher outlet temperature a bad thing if the block is actually cooler? Could the test be modified to utilize heat input and take multiple temperature measurements at different points in the system (Inlet/outlet of the heat exchanger. Inlet/Outlet of the heat source,and the casing of the heat source). Possibly a bunsen burner to a steel pipe section. Better thermal conductivity to give off heat means better to absorb heat as well. The pipe could be the "block" and the bunsen burner the "combustion" source. Would adding the water wetter reduce the temperature of the pipe once the system reaches steady state versus just plain water?
I see also in your test you want to use a pump with a known and consistent flow rate (which for your described test I completely agree with). Our water pump speed and thus flow rate will be affected by engine RPM as well. Now as a fluid moves faster through the system, it will not heat up as much, but the increased flow rate will transfer more heat out of the system due to more molecules passing in a given period of time. Is it simply the water wetter lowers viscosity and thus allows the flow rate to go up by reducing flow resistance? It works not by a change to the thermal conductivity, but increased flow? Given your pump has a steady state power, could we verify flow rate in the system as well... and again I would go back to how does this affect the actual temperature of the steel pipe, which is actually what would matter in a car.
I am by no means trying to convince you not to do a test. I think everyone on this thread would like you to do any level of testing that would provide a data point to determine is it "snake oil" or something that can help.
#47
Le Mans Master



Most testing is going to be challenged. If you ever do research and publish... that is exactly what an entire group of your peers will do. They will pick your test apart as they attempt to duplicate it, improve on it, or find something you missed. You will also see engineers and scientists sit around with colleagues and have these exact conversations until a team feels they have covered all variables before testing begins, even if it is only one person doing the testing. If you choose to ignore certain factors, you still need to address the rational of why they have no bearing on the test that is running.
So with your test... you are going to heat it up, let it flow and record time to drop from and to a specific T. Seems reasonable and should produce a meaningful data point establishing the heat transfer coefficient. But the Temperature will not be the same across the entire system. Obviously it will be cooler exiting the heat exchanger than entering it. Maybe it is better to record the time to reach room temperature at the heat exchanger's entrance?
Let's consider this though: This isn't really what happens in our car's cooling system. The heat source heats a medium that the water is then transferred through (Our Block). The goal isn't necessarily to have cooler fluid it is to have a cooler engine. The point where the temperature reading is taken in a cooling system is also meaningful. Pre/Post heat exchanger, up or down stream of the heating source, etc. If in the time the fluid is in the engine, it can absorb and carry more heat, is a higher outlet temperature a bad thing if the block is actually cooler? Could the test be modified to utilize heat input and take multiple temperature measurements at different points in the system (Inlet/outlet of the heat exchanger. Inlet/Outlet of the heat source,and the casing of the heat source). Possibly a bunsen burner to a steel pipe section. Better thermal conductivity to give off heat means better to absorb heat as well. The pipe could be the "block" and the bunsen burner the "combustion" source. Would adding the water wetter reduce the temperature of the pipe once the system reaches steady state versus just plain water?
I see also in your test you want to use a pump with a known and consistent flow rate (which for your described test I completely agree with). Our water pump speed and thus flow rate will be affected by engine RPM as well. Now as a fluid moves faster through the system, it will not heat up as much, but the increased flow rate will transfer more heat out of the system due to more molecules passing in a given period of time. Is it simply the water wetter lowers viscosity and thus allows the flow rate to go up by reducing flow resistance? It works not by a change to the thermal conductivity, but increased flow? Given your pump has a steady state power, could we verify flow rate in the system as well... and again I would go back to how does this affect the actual temperature of the steel pipe, which is actually what would matter in a car.
I am by no means trying to convince you not to do a test. I think everyone on this thread would like you to do any level of testing that would provide a data point to determine is it "snake oil" or something that can help.
So with your test... you are going to heat it up, let it flow and record time to drop from and to a specific T. Seems reasonable and should produce a meaningful data point establishing the heat transfer coefficient. But the Temperature will not be the same across the entire system. Obviously it will be cooler exiting the heat exchanger than entering it. Maybe it is better to record the time to reach room temperature at the heat exchanger's entrance?
Let's consider this though: This isn't really what happens in our car's cooling system. The heat source heats a medium that the water is then transferred through (Our Block). The goal isn't necessarily to have cooler fluid it is to have a cooler engine. The point where the temperature reading is taken in a cooling system is also meaningful. Pre/Post heat exchanger, up or down stream of the heating source, etc. If in the time the fluid is in the engine, it can absorb and carry more heat, is a higher outlet temperature a bad thing if the block is actually cooler? Could the test be modified to utilize heat input and take multiple temperature measurements at different points in the system (Inlet/outlet of the heat exchanger. Inlet/Outlet of the heat source,and the casing of the heat source). Possibly a bunsen burner to a steel pipe section. Better thermal conductivity to give off heat means better to absorb heat as well. The pipe could be the "block" and the bunsen burner the "combustion" source. Would adding the water wetter reduce the temperature of the pipe once the system reaches steady state versus just plain water?
I see also in your test you want to use a pump with a known and consistent flow rate (which for your described test I completely agree with). Our water pump speed and thus flow rate will be affected by engine RPM as well. Now as a fluid moves faster through the system, it will not heat up as much, but the increased flow rate will transfer more heat out of the system due to more molecules passing in a given period of time. Is it simply the water wetter lowers viscosity and thus allows the flow rate to go up by reducing flow resistance? It works not by a change to the thermal conductivity, but increased flow? Given your pump has a steady state power, could we verify flow rate in the system as well... and again I would go back to how does this affect the actual temperature of the steel pipe, which is actually what would matter in a car.
I am by no means trying to convince you not to do a test. I think everyone on this thread would like you to do any level of testing that would provide a data point to determine is it "snake oil" or something that can help.
I think you're right in that it would be more meaningful to tabulate entry and exit temps of the heat exchanger vs just tank temp.
Yea, when I do heat transfer modeling it is on the jacketed side to the process side... so generally the tank pressure doesn't impact as much because you're limited in heat transfer through the wall and mixing. Good catch and a big oof on my part lol.
And as far as peer reviewed, yeai don't have to deal with that yet. Generally I'm just the guy running the tests and then I give out a list of ways to modify the process for testing or prep so that you don't want to blow your brains out. Most of the stuff I do is for AASHTO procedures/testing though so there isn't as much of this in there.
I'm liking the feedback, here are the tweaks I'm working with so far:
I don't think the heated pipe will work, we would have too much variability there... however we could wrap a heating element around it with a controlled heat load on it perhaps.
Temps at inlet and outlet
Turbulent flow hopefully, going to crunch some numbers to figure that out.
Preheat the exchanger and pump... leave it at room temp for one hour then prime it by circulating the water through it for 1 minute to get to a psuedo steady state. Being the exchanger is aluminum that is probably a reasonable approximation. We could also just start when in=out roughly.
The flow rate change is interesting. We could assume the worst case scenario and build the pump flow rate at what the cooling system in the car would be at idle.
That's where I'm at so far. I need to go to sleep soon because I'm heading to a plant tomorrow though lol.
#48
Team Owner



If you don't want something that will be picked apart and challenged, try religion, any religion. Science will always be challenged. Come up with a law? Great. 50 years from now, someone could call it BS and prove it. Science is always having to be re-examined daily.
#49
Team Owner


Pro Mechanic
#50
Drifting



#51
Instructor


Member Since: Dec 1999
Location: Atlanta Ga
Posts: 161
Likes: 0
Received 0 Likes
on
0 Posts


I thought this only benefited race cars, my 88 get hot when driven under 30 mph ok on highway,
so I assume it it is a matter of airflow, even a racing radaiator & stewart water pump & bigger front pusher fan did nt help.
Does Dewitts fan help?
so I assume it it is a matter of airflow, even a racing radaiator & stewart water pump & bigger front pusher fan did nt help.
Does Dewitts fan help?
#52
Team Owner


Pro Mechanic

If you have a stock or stockish engine, then something else is wrong. It shouldn't get hot. First though...what are you calling, "hot"?
#53
Drifting



It seems people expect the cooling system to keep the car the same temp in traffic as it is on the highway. I see it in threads all over this board about how hot the LT1/LT4 runs. It's hot sure, but most are just having a false scare or a faulty temp sender/gage. The car itself is not operating out of expected design range.
Last edited by KyleF; 03-26-2019 at 10:17 AM.
#54
Team Owner


Pro Mechanic

I totally 
I think the bigger problem is that people get scared by the analog gauge; when the fan kicks on @~230, the gauge will look like it's just kissing 260...barely getting into the hash marks. To the unwitting, that would be concerning for sure. The rest of us have our DIC scrolled to temp display and can see that the thing is actually at 230 or less...or whatever it's really at.
You're right that it's almost always w/in the engineered range. But that itself is odd; from ~180 to ~230? That is a whopping 50* range that is "normal".

I think the bigger problem is that people get scared by the analog gauge; when the fan kicks on @~230, the gauge will look like it's just kissing 260...barely getting into the hash marks. To the unwitting, that would be concerning for sure. The rest of us have our DIC scrolled to temp display and can see that the thing is actually at 230 or less...or whatever it's really at.
You're right that it's almost always w/in the engineered range. But that itself is odd; from ~180 to ~230? That is a whopping 50* range that is "normal".

#56
Safety Car



I have a Very Hot running Corvette big block 427 and have learned a few tricks to keep it on the road without any "Events". I use an aftermarket BECooL Radiator which is all aluminum and works okay. After speaking to Tom at Dewitts I decided that my next radiator will come from them as they understand us folks with HOT running engines.
A CLEAN radiator is important. I have a standard BB Corvette Radiator right now but like anything aluminum it corrodes. I use a phosphoric acid spray to remove the corrosion from the aluminum. The fans that DeWitts sells are the same SPAL fans you see everywhere else to my knowledge.
Don't use too much antifreeze in your coolant, A/F inhibits the transfer of heat compared to the plain distilled water. I live in Virginia, here it got down to +5* (F) in the middle of the winter, I run 70 % Distilled water 30 % A/F in my coolant in my C4.
Use a good electric fan, don't try to get the 5 or seven blade AC blades on the water pump for cooling. I have a dual 11" Spal Fans on a shroud that covers the entire radiator and ity seals well. Good body seals are critical to keeping the car cool while moving.
A good fan controller makes a world of difference. I am using a DeRale PWM Type Electric fan controller which is very effective at keeping the engine at a preset temperature. The DeRale system works with a sensor mounted on the coolant return line and you can set the temperature at which your fans kick up to 100% speed. The fans start at 50% of their speed and speed up as needed to keep the temperature where you want it. Since I do not have AC in my C3 I use the A/C input for my manual override of the system.
A remote reservoir is installed to keep the Power Steering fluid at a reasonable temperature. This will help my power steering Rack and Pinion working longer with less heat.
If you don't like using additives that is your prerogative!
I would not say that they are "useless" or a waste just because you have not had experience with them. STP is actually from a recipe that we Stole from the Germans at the end of WW2. The original product was VERY good. The Germans had a problem with their aircraft getting the oil system shot up and the engines failed soon afterwards. STP was developed to allow the engines to continue running with ZERO oil pressure and make it back to the field. It worked when we brought it over.
The Snow Performance people make a great water/Methanol injection system. Where did the idea come from? The Germans again. They used the water/methanol injection to allow their fighters even more power when it was activated, it made their fighters even harder to shoot down as they would get an additional couple hundred horsepower for short bursts in the air while dog fighting. Smart ideas, Both of them and we have the Germans to thank for them.
I don't use STP but I would be careful about calling it a "snake oil". I use Red Line Water Wetter and I use it "because it works". I am an engineer as well and not given to trusting without testing a product. I am not a fool with too much cash, I simply try things that others have not. I have several patents on cooling systems because of my "open mind".
Stay Cool and replace that Radiator cap every five years for continuous protection from boil overs!
Regards,
Chris
A CLEAN radiator is important. I have a standard BB Corvette Radiator right now but like anything aluminum it corrodes. I use a phosphoric acid spray to remove the corrosion from the aluminum. The fans that DeWitts sells are the same SPAL fans you see everywhere else to my knowledge.
Don't use too much antifreeze in your coolant, A/F inhibits the transfer of heat compared to the plain distilled water. I live in Virginia, here it got down to +5* (F) in the middle of the winter, I run 70 % Distilled water 30 % A/F in my coolant in my C4.
Use a good electric fan, don't try to get the 5 or seven blade AC blades on the water pump for cooling. I have a dual 11" Spal Fans on a shroud that covers the entire radiator and ity seals well. Good body seals are critical to keeping the car cool while moving.
A good fan controller makes a world of difference. I am using a DeRale PWM Type Electric fan controller which is very effective at keeping the engine at a preset temperature. The DeRale system works with a sensor mounted on the coolant return line and you can set the temperature at which your fans kick up to 100% speed. The fans start at 50% of their speed and speed up as needed to keep the temperature where you want it. Since I do not have AC in my C3 I use the A/C input for my manual override of the system.
A remote reservoir is installed to keep the Power Steering fluid at a reasonable temperature. This will help my power steering Rack and Pinion working longer with less heat.
If you don't like using additives that is your prerogative!
I would not say that they are "useless" or a waste just because you have not had experience with them. STP is actually from a recipe that we Stole from the Germans at the end of WW2. The original product was VERY good. The Germans had a problem with their aircraft getting the oil system shot up and the engines failed soon afterwards. STP was developed to allow the engines to continue running with ZERO oil pressure and make it back to the field. It worked when we brought it over.
The Snow Performance people make a great water/Methanol injection system. Where did the idea come from? The Germans again. They used the water/methanol injection to allow their fighters even more power when it was activated, it made their fighters even harder to shoot down as they would get an additional couple hundred horsepower for short bursts in the air while dog fighting. Smart ideas, Both of them and we have the Germans to thank for them.
I don't use STP but I would be careful about calling it a "snake oil". I use Red Line Water Wetter and I use it "because it works". I am an engineer as well and not given to trusting without testing a product. I am not a fool with too much cash, I simply try things that others have not. I have several patents on cooling systems because of my "open mind".
Stay Cool and replace that Radiator cap every five years for continuous protection from boil overs!
Regards,
Chris
#57
Le Mans Master



So, any word on the test. I am very curious what the "Water Wetter" actually does.
Another excessive heat thread here
Another excessive heat thread here
#59
Team Owner



If you don't like using additives that is your prerogative!
I would not say that they are "useless" or a waste just because you have not had experience with them. STP is actually from a recipe that we Stole from the Germans at the end of WW2. The original product was VERY good. The Germans had a problem with their aircraft getting the oil system shot up and the engines failed soon afterwards. STP was developed to allow the engines to continue running with ZERO oil pressure and make it back to the field. It worked when we brought it over.
The Snow Performance people make a great water/Methanol injection system. Where did the idea come from? The Germans again. They used the water/methanol injection to allow their fighters even more power when it was activated, it made their fighters even harder to shoot down as they would get an additional couple hundred horsepower for short bursts in the air while dog fighting. Smart ideas, Both of them and we have the Germans to thank for them.
I don't use STP but I would be careful about calling it a "snake oil". I use Red Line Water Wetter and I use it "because it works". I am an engineer as well and not given to trusting without testing a product. I am not a fool with too much cash, I simply try things that others have not. I have several patents on cooling systems because of my "open mind".
I would not say that they are "useless" or a waste just because you have not had experience with them. STP is actually from a recipe that we Stole from the Germans at the end of WW2. The original product was VERY good. The Germans had a problem with their aircraft getting the oil system shot up and the engines failed soon afterwards. STP was developed to allow the engines to continue running with ZERO oil pressure and make it back to the field. It worked when we brought it over.
The Snow Performance people make a great water/Methanol injection system. Where did the idea come from? The Germans again. They used the water/methanol injection to allow their fighters even more power when it was activated, it made their fighters even harder to shoot down as they would get an additional couple hundred horsepower for short bursts in the air while dog fighting. Smart ideas, Both of them and we have the Germans to thank for them.
I don't use STP but I would be careful about calling it a "snake oil". I use Red Line Water Wetter and I use it "because it works". I am an engineer as well and not given to trusting without testing a product. I am not a fool with too much cash, I simply try things that others have not. I have several patents on cooling systems because of my "open mind".
Did we? I have done a brief Google search and nothing comes up except that the Afrika Korps used that in their gear cases for the Panzers. While I think the aircraft one is more colorful, I am not running a Messerschmitt Bf 109 engine in my car so I am not sure how to make that leap. Further to that, I am not even sure where the story comes from since it hasn't been on STP's website, colorful as it might be.
And the Allied forces used some sort of water injection to boost power. Good as either of them may be, it doesn't, even of the story of the STP stuff is true hasn't proven more than "Win a race on Sunday, sell a car on Monday".
I'm not doubting your ability as an engineer. I'm doubting a company that sells a product with wild claims and not have research to back it up. If they had a credible report from an accredited laboratory using acceptable testing methodology, sure. Other than that, what we have is an "UP TO" claim where any power gains including negative are probably within the "UP TO" limit.
#60
Team Owner


Pro Mechanic

THe "german airplanes" story doesn't jibe with WIKI's report; STP started in 1953.
An interesting quote from the article:
"In 1976, STP faced a consumer protection order that required it to have scientific backing for certain statements and prohibited making false claims. In 1978, it paid a $500,000 civil penalty over claims. In 1995, STP paid $888,000 to settle Federal Trade Commission charges of false advertising"
An interesting quote from the article:
"In 1976, STP faced a consumer protection order that required it to have scientific backing for certain statements and prohibited making false claims. In 1978, it paid a $500,000 civil penalty over claims. In 1995, STP paid $888,000 to settle Federal Trade Commission charges of false advertising"
