Centering Bellhousing Question...
#1
Team Owner


Thread Starter

This is/will be my first attempt at doing this...I have the dial indicator ready to attach....can/should i attach it to crank or offset it to flywheel?
And for reference its a small block..also is there a video i can look at for reference?
TIA
And for reference its a small block..also is there a video i can look at for reference?
TIA
#2
Team Owner




You tube has a few on this subject. Look in my thread about clutch not releasing and there are a couple link in there.
#3
Melting Slicks



been there very recently, never done it before!
You can read my findings and pictures in this thread post 24 https://www.corvetteforum.com/forums...-repair-2.html
A great 'how to' article is here http://www.hurst-drivelines.com/wp-c...d-6-15-09A.pdf
It took offset dowels to get it right.
video I liked was this one
You can read my findings and pictures in this thread post 24 https://www.corvetteforum.com/forums...-repair-2.html
A great 'how to' article is here http://www.hurst-drivelines.com/wp-c...d-6-15-09A.pdf
It took offset dowels to get it right.
video I liked was this one
#4
Team Owner


Thread Starter

The problem im having is centering the dial up to hit the edge....just can't figure out the combo of all the moving parts..its a real 'pia' when its still in the car...

#5
Melting Slicks



Jack, it has to attach to the flywheel face,,, the crank will give you bad readings. I struggled, and finally I purchased the slip-fit alignment tool.... Waiting to get the engine off the cradle to use it.
#6
Melting Slicks



I centred it without pressure plate, clutch. Magnet base dial mounted on the crankshaft flange.
#7
Melting Slicks


#8
Melting Slicks



There isn't enough face on the crank for the magnet to attach and travel in a circle....it can only attach to the face of the flange where it travels in an ellipsis . You need the base to rotate around the axis of the crank, not rotate with the crank..if that makes sense...
#9
Team Owner


Thread Starter

I got the magnetic base one...flywheel still attached...it attaches but when i try to move the arms for adjustment the damn thing comes loose and I am getting frustrated....
What is a 'slip fit tool' and what does it look like?
What is a 'slip fit tool' and what does it look like?
#10
Melting Slicks



It bolts to the crank flange and has a ring that slips on..if it passes thru the bell housing it aligned correctly.
https://www.google.com/search?q=bell...2sruF2ZMz6M%3A
https://www.google.com/search?q=bell...2sruF2ZMz6M%3A
#11
Team Owner


Thread Starter

It bolts to the crank flange and has a ring that slips on..if it passes thru the bell housing it aligned correctly.
https://www.google.com/search?q=bell...2sruF2ZMz6M%3A
https://www.google.com/search?q=bell...2sruF2ZMz6M%3A
OUCH...I cannot justify spending that type of $$$$ for a one time use...
Last edited by 66jack; 08-23-2015 at 01:53 PM.
#12
Melting Slicks



There isn't enough face on the crank for the magnet to attach and travel in a circle....it can only attach to the face of the flange where it travels in an ellipsis . You need the base to rotate around the axis of the crank, not rotate with the crank..if that makes sense...

#13
Race Director


Member Since: Feb 2007
Location: northern california
Posts: 13,617
Received 6,538 Likes
on
3,007 Posts
C2 of Year Finalist (track prepared) 2019


To center the hole in the bell housing on the crank axis with a dial indicator that has a magnetic base, just stick it to any portion of the flywheel which provides a stable mount. Of course, use offset bellhousing dowels to shift the bellhousing up/down, left/right as needed.
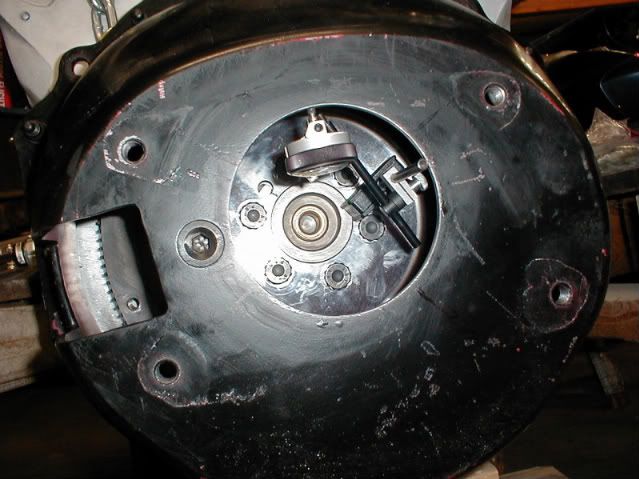
After you have the bellhousing centered, put the tip of the dial indicator on the transmission mounting surface of the bellhousing and verify that the bellhousing is perpindicular to the crank axis. Use shim stock between the bellhousing and the block to change the angle of the bellhousing, if needed.
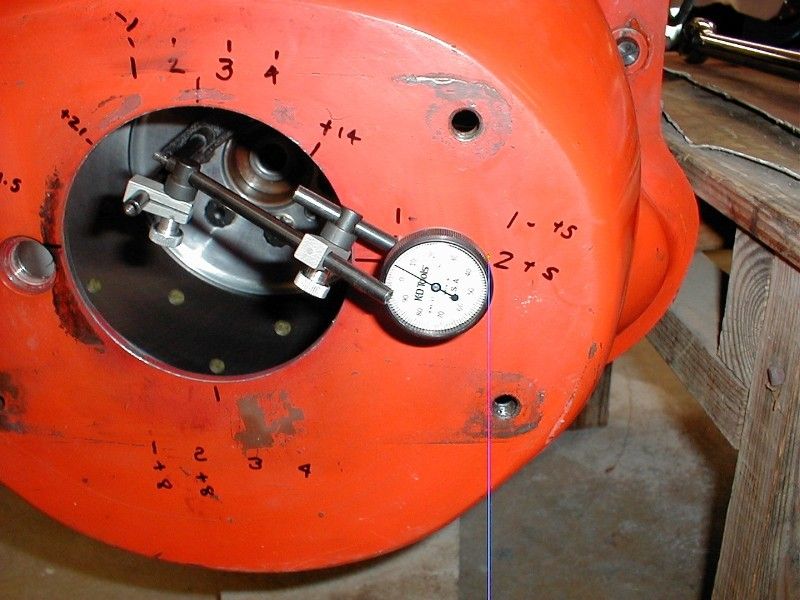
And that's pretty much what you can do with the engine in the car and the bellhousing attached to the block. With the bellhousing off, though, you can mount the dial indicator stand on the block and use the tip of the dial indicator to check for flywheel run-out. Sorry no picture.
Overall, this is not a fast process, but neither is it difficult.
Jim
#14
Melting Slicks



while you are it, the problem I encountered may be of interest.
After aligning the bell (without the clutch in place) the gearbox went in like a dream for a test fit. Then, I unmounted everything, installed the pressure plate and the clutch (using the clutch alignement tool), reinstalled the bell housing and ..failed to get the gearbox slide back in. I think I mounted/unmounted 4 times (everything, including clutch&Co!) to see what I did wrong. Finally I found the alignement tool (that came with the gearbox kit) to be the problem. The fit in the pilot bushing was too loose (only slightly) , and the pressure plate assembly dropped somewhat under gravity before tightening the bolts. Result: everything was aligned , but the clutch disk (with the slots that grab over the gearbox axle) was not. So the slots blocked against the gearbox axle rather than slipping over it. I put some thin tape over the tip of the alignement tool to have it tight fit in the pilot bushing, and voila, problem resolved
But even then slipping the gearbox in needed a delicate handling. The tip of my gearbox axis is chamfered (RS400), and the very sharp chamfered edge acts like a chisel on the soft metal of the pilot bushing. I read many posts where people start wiggling the gearbox until it fits, I am afraid that does not work without damaging the pilot pushing. I rounded that edge off to take out its sharpness, and the box went in much more easily
After aligning the bell (without the clutch in place) the gearbox went in like a dream for a test fit. Then, I unmounted everything, installed the pressure plate and the clutch (using the clutch alignement tool), reinstalled the bell housing and ..failed to get the gearbox slide back in. I think I mounted/unmounted 4 times (everything, including clutch&Co!) to see what I did wrong. Finally I found the alignement tool (that came with the gearbox kit) to be the problem. The fit in the pilot bushing was too loose (only slightly) , and the pressure plate assembly dropped somewhat under gravity before tightening the bolts. Result: everything was aligned , but the clutch disk (with the slots that grab over the gearbox axle) was not. So the slots blocked against the gearbox axle rather than slipping over it. I put some thin tape over the tip of the alignement tool to have it tight fit in the pilot bushing, and voila, problem resolved

But even then slipping the gearbox in needed a delicate handling. The tip of my gearbox axis is chamfered (RS400), and the very sharp chamfered edge acts like a chisel on the soft metal of the pilot bushing. I read many posts where people start wiggling the gearbox until it fits, I am afraid that does not work without damaging the pilot pushing. I rounded that edge off to take out its sharpness, and the box went in much more easily

Last edited by alexandervdr; 08-23-2015 at 04:35 PM.
#15
Team Owner


Thread Starter

Like i said...first time trying this and I still cant figure out the combo to get this thing to work...the shaft on the holder is too long to attach to flywheel...it hits the bell housing, if i try and attach to crank I cannot get the combo of angles....
I'm giving up for today......4 hours of frustration and nothing to gain...

I'm giving up for today......4 hours of frustration and nothing to gain...

#16
Race Director


Member Since: Feb 2007
Location: northern california
Posts: 13,617
Received 6,538 Likes
on
3,007 Posts
C2 of Year Finalist (track prepared) 2019


Like i said...first time trying this and I still cant figure out the combo to get this thing to work...the shaft on the holder is too long to attach to flywheel...it hits the bell housing, if i try and attach to crank I cannot get the combo of angles....
I'm giving up for today......4 hours of frustration and nothing to gain...

I'm giving up for today......4 hours of frustration and nothing to gain...

#17
Race Director



Member Since: Nov 2000
Location: Beverly Hills (Pine Ridge) Florida
Posts: 10,152
Received 526 Likes
on
375 Posts


You need a different set of shafts / extensions for the magnetic base, and maybe a different magnetic base and dial indicator.
I ran into the same thing when I recently did a bell housing. My "good" magnetic base and fixed rod (on the base) was too long, so I had to use my old lower profile base & rods. Those rods are thinner, so the wgt. of the dial indicator is important (a heavy dial indicator may cause the indicator to move or cause the magnetic base to loosen / move).
Recommend the McRobb offset pins, if you need them.
Good luck,
Plasticman
I ran into the same thing when I recently did a bell housing. My "good" magnetic base and fixed rod (on the base) was too long, so I had to use my old lower profile base & rods. Those rods are thinner, so the wgt. of the dial indicator is important (a heavy dial indicator may cause the indicator to move or cause the magnetic base to loosen / move).
Recommend the McRobb offset pins, if you need them.
Good luck,
Plasticman
#18
Team Owner


Thread Starter
#19
Race Director



Some folks use steel flat stock about 1.5 inches x 4 inches x 1/8 inch thick to make a "bridge" piece that goes across the crank flange to provide a secure center mount for the dial indicator base. Drill a couple of holes in it to mount it securely to the crank flange/flywheels bolts. This allows you to center the dial indicator mount without any wobble or misalignment.
A few years ago, I put together a presentation for NCRS on doing these bell housing checks and corrections. I used my own personal experiences as well as two or three of the best videos out there to put together a "best practices" way to do this job without issues or hassles. Designed for the novice, but also good for experienced guys. If you want or need a copy let me know. The procedure itself is less than 1 MB, but with all the pictures is around 30MB...............a bit much to email. But let me know if I can assist.
Use of the Browell alignment tool is also discussed as a second way to do this job. But I like the standard dial indicator method for occasional/infrequent use.
I also agree with Plasticman on use of the McRobb offset dowels.....................use them and not the others.
Larry
Last edited by Powershift; 08-23-2015 at 07:09 PM.
#20
Team Owner


Thread Starter

Jack:
Some folks use steel flat stock about 1.5 inches x 4 inches x 1/8 inch thick to make a "bridge" piece that goes across the crank flange to provide a secure center mount for the dial indicator base. Drill a couple of holes in it to mount it securely to the crank flange/flywheels bolts. This allows you to center the dial indicator mount without any wobble or misalignment.
A few years ago, I put together a presentation for NCRS on doing these bell housing checks and corrections. I used my own personal experiences as well as two or three of the best videos out there to put together a "best practices" way to do this job without issues or hassles. Designed for the novice, but also good for experienced guys. If you want or need a copy let me know. The procedure itself is less than 1 MB, but with all the pictures is around 30MB...............a bit much to email. But let me know if I can assist.
Use of the Browell alignment tool is also discussed as a second way to do this job. But I like the standard dial indicator method for occasional/infrequent use.
I also agree with Plasticman on use of the McRobb offset dowels.....................use them and not the others.
Larry
Some folks use steel flat stock about 1.5 inches x 4 inches x 1/8 inch thick to make a "bridge" piece that goes across the crank flange to provide a secure center mount for the dial indicator base. Drill a couple of holes in it to mount it securely to the crank flange/flywheels bolts. This allows you to center the dial indicator mount without any wobble or misalignment.
A few years ago, I put together a presentation for NCRS on doing these bell housing checks and corrections. I used my own personal experiences as well as two or three of the best videos out there to put together a "best practices" way to do this job without issues or hassles. Designed for the novice, but also good for experienced guys. If you want or need a copy let me know. The procedure itself is less than 1 MB, but with all the pictures is around 30MB...............a bit much to email. But let me know if I can assist.
Use of the Browell alignment tool is also discussed as a second way to do this job. But I like the standard dial indicator method for occasional/infrequent use.
I also agree with Plasticman on use of the McRobb offset dowels.....................use them and not the others.
Larry

Pictures are better for me...I, at times have problems visualizing...
